3 Steps Towards Home Energy Efficiency
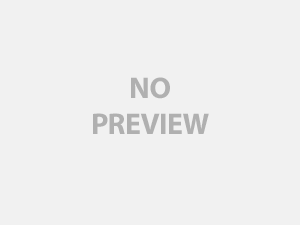
The following are the steps that Genesee Crest Ltd recommends that a home owner follow in order to make their home more energy efficient. If your home is in fairly decent to good condition, you can basically follow the steps in the order presented. Depending on your circumstances and funds available you may have to skip around. For example, if you have a window that is in bad shape and limited funds, skip insulation and fix the window.
Step One – Sealing leaks for energy efficiency
The first thing that a home owner can look at is the sealing of any air leaks in the exterior of the home. I recommend starting with the foundation of your home. If you have a block or concrete wall foundation, inspect the foundation for cracks. For a block foundation, inspect the mortar between the blocks for cracks. Any crack large enough that you can fit a penny into it should be repaired. Your local hardware store will carry a product for hydraulic mortar repair. Follow the directions on the container, mixing it with the appropriate amount of water and stuff if into the cracks of your mortar. If a crack extends below the ground it would be a good idea to dig down and repair the entire crack line. Depending on the condition of your foundation it may be a good idea to get a contractor to take a look at it. If you have a history of water getting under your home or in your basement, now is a good time to dig up the foundation, seal it with black tar and install a foam insulation like polyisocyanates (available at your local lumber yard) to the exterior.
The next step towards sealing your home for energy efficiency is to start at the sill plate (right above the foundation) and work your way up the siding, inspecting for possible air leaks. Any cracks that might allow air to move from the inside out and vice a versa, should be sealed with a quality caulking. I personally recommend always using a caulk with 35 year guarantee or better that is paintable. Simply put, the better the guarantee, the longer the caulk lasts and the less amount of times you have to go through this. Pay particular attention to cracks in wood, between wood, around windows and doors. If your windows and, or doors look like they may need replaced and you will be able to replace them in the near future, Do Not Caulk Them. Replacing a door or window that has been firmly caulked in can be a lot more work. On the other hand if you can’t get to replacing them in the near future, caulk them well.
Step Two – Insulating for energy efficiency
A typical home in my area, close to Lima Ohio, is over 100 years old and has walls that are insulated in the area of about R-11 to 13 with a ceiling or roof insulation of around
R-19. Summer temperatures in my area reach over 90 degrees and winter temperatures regularly get down below freezing and single digits. R-11 walls and R-19 ceilings are, simply put, a joke when it comes to energy efficiency.
The first thing a home owner should do is evaluate your homes insulation. If you live in an area similar to mine, I would recommend trying to get close to R-40 in the walls and R-60 in the ceiling, super insulated. Now that could be a far reach both physically and financially, but I would go for as much insulation as you can.
The first step is to evaluate the insulation in the ceiling or attic of your home. Unless you have no insulation in the walls of your home I would recommend putting every penny you can possibly afford into the insulation of your attic. Either blow in insulation or lay bats of fiberglass insulation in the attic until you get to R-60. When you shop for insulation the R value is stamped on each bat of fiberglass. Each bag of cellulose fiber for blowing in will tell you how many inches to spray to get to the desired level. Ensure that you follow the directions on the bag for installation.
The next step is to evaluate the existing walls of your home. Is there any insulation in them? Believe it or not, in my area you can still find wood frame homes without insulation in the walls. If that is the case you can hire a contractor to blow in insulation or if you are handy, do it yourself. Stores like Lowe’s will sell you the insulation and provide a machine for pumping it into your walls.
At this point the average home will have walls insulated to approximately R13, a long way to go to R-40. The easiest way is to double the thickness of the exterior walls of your home. If you have large interior rooms the cheapest way is to frame a 2″ X 6″ interior wall right next to the existing walls. Some electrical and plumbing work will be needed to extend those fixtures to their new locations. As a do it yourself project, you can install fiberglass insulation or a contractor can blow in foam insulation. The foam will carry a higher R-value if you can afford it. Install new drywall and finish. At this point with fiberglass insulation you will have a wall that is insulated to at least R-32. If you have the money and space you can also install sheets of polyisocyanates. Polyisocyanates is an extremely energy efficient material that in 1/2″ X 4′ X 8′ panels is
R 3.3 per Ã?½.”
If you don’t want to lose square footage on the inside of your home you can basically do the same thing on the exterior of your home. This also works best if you also are in need of new siding of the exterior of your home. The most expensive method is to pour a new foundation next to the existing foundation. Frame up new walls, insulate and install new siding.
If framing up walls on the interior or exterior of your home is not something you would prefer to do, the only method left is to install a quality board insulation like polyisocyanates to the exterior and reside. This is a job that most would not do as a do-it-yourself project. If you install 2″ of polyisocyanates and then side the home, you will have added R-13 to the walls, in effect at least doubling their energy efficiency. Although not the most energy efficient, this method is probably the most practical for the average homeowner.
Step Three-Energy efficient doors and windows
The third step in our quest for making our homes more energy efficient is to take a look at what kind of doors and window we have. If you have old single pane windows, then it is time to replace them. If your windows are that old, your doors probably are in need of replacement also. The main thing to look for in doors and windows are: Energy Star Rating, insulation and low-e. Like the appliances in your home, your windows and doors should be rated for your area of the country by Energy Star. Vinyl frames for windows and the doors themselves should be insulated. The glazing on the doors and windows should be double pane with a low-e coating and argon or krypton filled. Triple pane with two low-e coatings and argon or krypton filled is preferable, but not really cost effective at this time.
I personally recommend that for installing doors and windows, if you have no experience doing it, hire a contractor. Let the contractor take the measurements and order the windows for you. That way if there is a problem with an incorrect size, or an opening is out of square, you have a professional that is used to dealing with these sort of problems. If you measure for new windows, order them and the size is not correct, you are stuck with the windows.
Follow these three simple steps and your home will be more energy efficient. It used to be considered cost prohibitive to do “green” remodeling and construction. Not so today. Although the cost associated with green remodeling and achieving an Energy Star Rating for your home is higher than that of traditional remodeling and construction, the cost of operating a home with an Energy Star Rating is 10-20% lower. Energy Star rated homes and buildings also sell for an average of $61 per square foot more than comparable buildings. Commercial buildings with a LEED (Leadership in Energy and Environmental Design) rating sells for an average of $171 per square foot more than comparable buildings.