DIY: How to Make a PVC Camping Cot
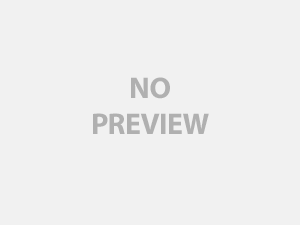
You don’t have to be Goldilocks to find a camping cot that’s “just right.” Commercial cots tend to be narrow, way too long or too short. They are made to fit average sizes, although I’ve met very few “average” people.
Camping is one of my favorite hobbies. Camping cots are not. The aluminum types tend to be too flimsy, too heavy, too big or other problems. I’ve purchased models that when assembled, the fabric bed would not fit into the frame at all. Returning them to the store is a pain.
Since another hobby of mine is working with PVC, I had an idea that hit just right.
I designed a PVC camping cot and bed that works perfectly. It’s lightweight, stores quickly and costs almost nothing. Best of all, the design can be customized for any one of any size.
I made mine out of 1″ PVC pipe and connectors. I like using schedule 40 PVC, which is made to withstand high water pressure. It’s thicker and stronger than regular furniture grade PVC pipe.
Children’s cots can be made from ¾” PVC pipe, while people who weigh 200 lbs. and over should use 1 ½” to 2″ PVC pipe. For heavier folks, I would double the cot fabric.
It is assumed that the builder has knowledge of sewing and basic hand tool use. Books and online sites are available with free instruction, or one ask or trade with friends with skills.
You will need:
- · Four three-way PVC connectors
- · Four PVC poles (these are sold in 10′ lengths at any DIY store)
- · Drill with bits
- · Four each 2″ long 5/8″ carriage bolts
- · Four each 5/8″ cap nuts
- · Eight each 5/8″ washers
- · Four each PVC pipe end caps
- · Heavy duty outdoor fabric
- · Heavy duty sewing thread
- · Sewing machine and sewing tools
- · Hacksaw
- · Sandpaper, medium to fine
- · Marking tools and tape measure
- · PVC cement
Step One:
Instead of measuring myself for my new cot, I measured twin beds at a mattress store. To make myself look more like a customer, I laid down on the beds and stretched out. I decided I could sleep within the measurements of a twin.
I knew a friend had a twin air mattress, so I borrowed it for a weekend and slept on it. It was considerably thinner than the conventional mattress.
An internet search revealed several models of air mattresses, all with different widths.
Eventually, I hit on the formula that worked for me. I would make a bed that allowed an air mattress to fit on top of the fabric without sitting on or sliding on the frame. My new twin air mattress measures 39″ wide by 74″ long by 5″ high. My bed measures 43″ wide by 77″ long. The height of the mattress does not matter.
If I decide to use the bed without an air mattress, I can lay on the fabric bed comfortably.
Step Two:
I cut two pieces of pipe, each 77″ long. This made the sides. I cut two pieces of pipe, each 43″ long. These are the head and foot pieces. Enough length was added to fit into the connectors.
I placed each pipe into a three-way connector with the open connectors pointing down. I made sure the frame was lying on a flat, level surface. I made a mark on each connector and pipe. I drilled a hole through the side of each connector to the inside of the frame. Ensuring each pipe was inserted all the way in was essential. I threaded washers onto each carriage bolt, inserted them through the holes to the inside, threaded another washer onto the bolts and finished with cap nuts. This allows the frame to be picked up and carried. The most vigorous sleeper cannot make the bed shake apart.
Step Three:
The length of bed legs will depend on the builder. I cut four pieces of pipe, each 24″ long. I cemented an end cap onto one end of each pipe.
I inserted each pipe into the three-way connectors. It looked good. For added strength, additional carriage bolts can be inserted through each leg.
Step Four:
I measured the width and length of the bed frame and added enough for a fabric sleeve on each end. The corners of the cut rectangle is cut away and reinforced with bias tape made from the fabric.
For strength in the seams, I used triple stitching on the seams. Since I like to go “slightly” overboard as my friends like to joke about, I used heavy duty duck canvas. It is easily waterproofed and wears like iron.
Casings at each end and sides allow the pipes to slide through. Making the inside measurements a little narrow, ( used ¼”), allows the fabric to fit tightly. It will be long while before the fabric stretches and becomes loose.
The bed was now ready to use. I gathered denim scraps and created a custom made duffel bag to hold my new bed, and created a wallet from two jeans pockets. I sewed them together and inserted a zipper at the top. This holds the carriage bolts, washers and cap nuts.
Since the bed is not cemented together, it breaks down for easy carrying and storage. Paint or stain your bed any color you wish. Mine is bright yellow.
Make one for yourself, and for friends and family. They make great gifts. If any one somehow breaks one, they are not expensive to replace.
Source: The author of this article has over 40 years of experience in diverse forms of DIY, home improvement and repair, crafting, designing, and building furniture, outdoor projects and more.