The Benefits of a SIPS Built Home vs Stick Built Homes
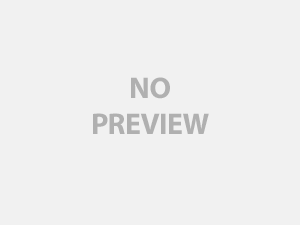
Insulation plays an important part in creating a comfortable home, and choosing the right insulation can cut energy costs in half. In stick built homes, the traditional method is batt insulation, but more builders are recognizing the benefits of building with structural insulated panels (SIPS). Using SIPS can not only cut your heating and cooling costs by a minimum of 50%, they can also shave days off of building time and cut labor costs. Comprised of recyclable materials and reducing energy usage, SIPS are an environmentally friendly way to go as well.
Gary Ruth, general contractor and owner of The House That Ruth Built, is using SIPS for the first time on a residential home and is pleased with the benefits he has found. SIPS can be pre-cut at the plant, which saves time and money on carrying and installation costs. He said that the panels fit together like an “old fashioned erector set”. They seal the house off so that there are no leaks, which helps remove drafts and keep out external noise. He also said that batt insulation is inherently flawed. In stick built homes, any variants in the gaps between the studs, like a bow, mean that there can be a cold air spot.
“You’ll find those in most stick built houses,” he said.
According to Ruth, another reason many people pay higher energy billsÃ?¯Ã?¿Ã?½is they have attached or “built in” garages which are not usually super insulated. This creates a huge cold spot in a house and makes the HVAC system work harder, resulting in higher energy bills. Building a SIPS house can remove that problem. Ruth also said that to further improve efficiency, builders can use larger SIPS.
“Wood does zero for insulation,” he said. “So, the further apart you put 2 x 4’s, the better. Using larger SIPS means less 2 x 4’s, which means less chance for a cold spot.”
SIPS not only provide more efficient insulation, but stronger houses as well. SIPS are made of two sheets of high tech plywood of Oriented strand board (OSB) with expaned polystyrene foam (EPS) laminated between them. This allows the SIP to perform as an I-beam. They combine framing, sheathing and insulation into one step, which allows SIPS homes to be built up to 30% faster than stick built homes. This means more savings on labor costs for the builder.
“Basically, this means that you can hang pictures or decorations any where without having to look for a stud,” said Ruth. “Externally, the masons doing the brick or stone on stick built homes have to look for studs to tie into. With SIPS, they can attach their work anywhere.”Ã?¯Ã?¿Ã?½
Ruth said that he can not stress how often people want the maximum square footage for the least amount of money and just “go with the cheapest option”. He said that by just making a few sound decisions up front, they can save enormous amounts of time, have better quality, and enjoy savings for years to come.
Others are Reading
Posted by john in Decorating & Design