Operations Management
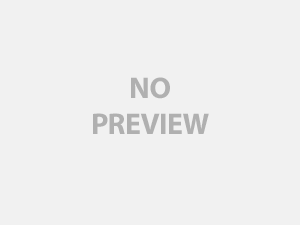
Of all the control charts and performance matrices, a Pareto chart is deemed very effective in that it analyzes potential process problems by sorting the attributable factors from highest to lowest percentage of some sum total (Control Charts). It is very useful when trying to determine which criteria are most relevant to the process variation, or when trying to find what are the largest challenges to overcome when rectifying negative process variation. For example, a hospital may use a Pareto chart to identity the reason for a high mortality rate among its patients, or in the instances that patients are not receiving their medications on time or at all.
Attribute control charts have the advantage of allowing for quick summaries of various aspects of the quality of a process, that is, the manager may simply classify parts of the process as acceptable or unacceptable, based on various quality criteria. Thus, attribute charts sometimes bypass the need for expensive, precise devices and time-consuming measurement procedures. Also, this type of chart tends to be more easily understood by managers unfamiliar with quality control procedures; therefore, it may provide more persuasive evidence of quality problems to management. Operations Managers must be very analytical and decisive in determining which input resources are best for the final output product/service.
Operations Managers must make decisions that can be broken into 3 categories-strategic decisions (long term), tactical decisions (intermediate-term), and operational planning and control decisions (short-term) (Moore 135). Strategic decisions are usually the decisions the company will have to live with for an extended period of time. Issues such as where do we establish the business, or the location of new organizational subsidiaries (Lopez, Blum, and Barnes 364). Tactical decisions focus on the human and capital resources of the organization and how they are to be distributed in the midst of the strategic decisions (Lopez, Blum, and Barnes 366). Examples of tactical decisions would be determining how many employees are needed to efficiently run the organization, and which types of materials are needed to effectively produce the most valuable product. Operational planning and control decisions are more focused on what is happening in the here-and-now. This level of operational management decisions addresses issues such as what issues do we work on today, or what projects will be managed this week and what is the best way to manage such projects.