Choosing the Correct Hammer
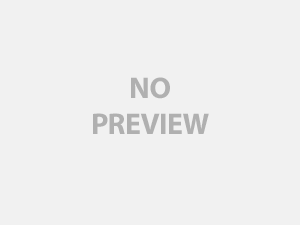
Apart from the way these are made, hammers also come in a variety of patterns, each with its own purposes.
Claw hammer This head has a split end, or claw, for pulling out nails. Use the handle as a lever once the nail is gripped.
Pin hammer This is a light hammer for driving panel pins, fine nails and tacks. The head is flat at the back for starting small nails.
Cross pein A larger version of the pin hammer, it comes in a number of patterns, of which the commonest is the warrington.
Ball pein The ball-shaped pein at the back of the head is used for beating metal or for setting rivets.
Club hammer This has a heavy steel head up to 1.8 kg (4lb). Use it to hit a steel chisel or bolster, or hand-held masonry-boring tool. Wear protective gloves and goggles.
Soft-faced hammer The head usually has a different material, such as copper, rubber or nylon, on each face. One of the most useful is a hammer with one soft and one hard rubber face.
Mallet (joiner’s or carpenter’s) The head is flat face and usually made of beech. Its main job is to hit chisels with wooden handles.
Sledgehammer This has a heavy head up to 9kg (20lb) with a long handle for heavy driving. Flat-faced, ball-pein or straight-pein types are available. Light blows can be made by holding the hammer just below the head and dropping the head onto the object to be driven. For heavier blows, hold it near the end of the shaft and swing it like an axe.
Repairing a hammer
Loose head On older hammers the shaft may shrink, or steel or hardwood wedges may have worked loose. If wooden wedges are loose, remove them, apply waterproof wood glue and tap back in place. With steel wedges, push slivers of hardwood into the holes, and then hammer back the wedges.
Damaged shaft If the handle is cracked or badly damaged, clamp the hammerhead in a vice and drill holes in the handle to weaken the grip of the wedges holding it in place. When possible, wiggle out the remaining wood. If it will not move, chisel it out with a thin wood chisel and mallet.
Take the hammerhead to your tool shop and get a new shaft of suitable size. It may need some sandpapering down to make it a tight fit. If the handle is not cut to take wedges, grip it in a vice and make saw cuts in the top end, slightly deeper than the depth of the wedges. Put the head on the shaft, and then tap the other end of the shaft firmly against a hard surface to drive the head onto the handle. Saw off any excess wood above the head, and then drive in the wedges until they are flush with the end of the handle.