The Basics of Slip Casting Ceramics
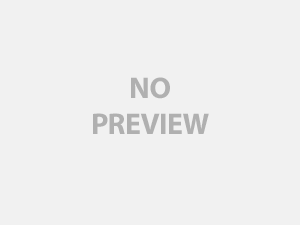
You can buy clay slip from your local ceramic shop or even order it online from art and craft stores if you can’t find it locally. Be sure to read the description of the slip to ensure that it is suitable for the project that you want to use it for. Some slips like porcelain slip require firing in the kiln at higher temperatures while normal ceramic slips can be fired at lower temperatures. If you are doing a particularly large ceramic project you will also need to keep that in mind since some clays perform better for large projects than others. If you have any doubt about what type of clay slip to purchase for your project either ask the salesman at your local store or email the owner of the website where you are ordering your slip and they should be able to help you find the right kind.
Once you have purchased your slip you will need a ceramic mold. Ceramic molds are made of plaster which helps to pull water out of the slip. You can buy a variety of different ceramic molds online. For new ceramic molds check out any of the ceramic stores. If you want to find some cool vintage ceramic molds you can always check out eBay or even look in your local classifieds. One of the great things about plaster ceramic molds is that they often last for years so you can find some really interesting older pieces to slip cast and create unique items. You will also need bands or straps to hold the mold closed.
First, strap your mold together. Then, stir your slip to make sure it is evenly mixed and pour the slip into the mold, filling it to the top. Once the slip has been poured into the mold the plaster of the mold will begin pulling the moisture out of the outer layer of slip and forming the walls of your project. The longer the slip stays in the mold the more moisture is pulled out and the thicker the walls of your project will be. If you leave it in there long enough eventually the piece will become solid all the way through with no liquid in the middle (which usually is NOT what you want). The trickiest part of slip casting is knowing when to dump the excess slip out of the mold to stop the wall thickness from increasing. If you dump it out too soon the sides of your project will not be thick enough and it will be too fragile. If you wait to long the sides will get too thick.
Typically you should wait to dump the slip until the walls are between 1/8″ – 1/4″ thick. The thickness of the wall will vary depending upon the size of the piece. Usually smaller pieces should have thinner walls. Once the walls have reached the right thickness, dump the excess slip out of the mold through the pour hole. Place the mold upside down over a bowl to allow any extra slip to drip out. Leave the mold to allow the clay to harden enough to be removed from the mold. The time on this will vary depending upon the size of the piece, though usually about 15 minutes is long enough for small pieces.
To remove the mold, trim off any excess clay around the top of the mold and place the mold on its side on a flat surface. Gently try to remove the top half of the mold. If it feels like it is sticking at all then the clay needs longer to dry. Leave it for another 5 minutes or so and try again. If the mold comes off easily, allow the piece to set with just half of it exposed for another few minutes to help it firm up before removing the other half. After a few minutes turn the piece over holding it gently in your hand – if it still feels soft give it a few more minutes to dry. Otherwise, remove the other half of the mold.
Once your piece has been removed from the mold allow it to dry overnight and then clean it up for firing. Keep in mind that all time estimates in the articles are approximations and not hard and fast rules. The time you will need to leave the slip in the mold will vary greatly depending upon a number of factors ranging from how large your piece is to the temperature and humidity of your location. The good thing is that slip is fairly inexpensive so you can experiment until you get the technique down without going broke in the process.