Trakkin on Main Street, Episode 2
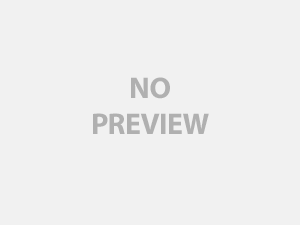
Fast forward from re-bar moving to a flatbed in the usual space alongside the trolley tracks. This time, the truck’s got packs of bricks for the front of the building, which has by this time, managed to grow 5 floors. There are five bays across, with scaffolding across three of them, with workers putting bricks across the fronts of them, sealing them off to any more hardware or material loading we might have done. With the remaining two bays, we loaded up sheetrock, hardy board, and any other materials needed inside to finish out what will eventually be condos.
Back to the truck, and the bricks. These packs have two narrow holes in each pack, two bricks wide, two bricks high, and only about 4 bricks between them. We had put on some narrower forks for this, but had to watch for depth, so the forks wouldn’t tear up the packs behind what I was picking up. On the mall, where there isn’t much there but track for the trolleys, and brick, which doesn’t make for a smooth ride. The surface made it absolutely necessary to carry very slowly, so as not to jostle the packs, and break them up in transit to the storage point. Once there, the wide mast made it necessary to complete a row, two high, before putting another in front. The load was tilted back a little, so it had to be flattened out, so the forks could come out without grabbing a brick and bringing the whole pack back with it. This was very meticulous work, especially on the upper levels.
Now after the truck was unloaded, a 2 hour exercise, there was this issue of putting bricks up unto the scaffolding, where the bricklayers were. Now the building sits in one block, on the west side. Across from it is another building, and the next block south, same side is a big hole, waiting for a building. This hole has fence in front and around. The bottom of the hole is a hard enough surface for most of the construction workers to park. Along the front, is the fence, and a lot of building material, whatever we could not put into the building. First the brick, then construction naterials, then a large area for the sheetrock. So, the brick stockpile sits cattycorner to the building site, close, but not too close. In front of the building there was a large sandpile, a water hose, several bags of mortar compound, and a mixer. To keep the mixer onsite, the contractor took off one of its wheels.
The two most unnerving parts of this whole business were getting bricks and the mortar box into the scaffolding, without incident. Every day had several loads of each to put in place. It went like this: Pick up the pack, drive it around to the scaffold, get far enough uphill to let the trollley get by behind me, put down outriggers, lift the load up to its parking place, put it there, and get the forks out without bring the load back down with you. Parking the load in place really wasn’t hard. Loading in down low wasn’t too bad, either. The forks were fairly close to level, and came straight back when you pulled them back. Let the work get higher up the building, and it became a whole new ballgame. Being at angle, the boom wants to bring the back of the forks down when you started backing out. This meant inching out. Otherwise the downward pressure forced the tips up, snagging the load at the back, at the top of the hole.
Soooo, it was pull the boom, raise the boom, pull more, raise more, until you had it out of the load, and the load didn’t come with you. This was done in about 6-inch motions, with hand signals. Didn’t matter that you couldn’t understand words, you lived (and died) by hand signals. This was very stressful with brick packs, less so with the occasional mortar bucket load-ups. The bucket sat on feet about 6 inches high, so it was easier to get out of. Still, they always had me park it near the edge, never in very far, so the feet had to be left on wood, or the front of the place was a mess of mud! Never happened, I am proud to say.But one time, I did come out after a mortar load up, up high, and did not get the boom low enough to clear the trolley wires. The main forks had been wired back to the mast, with the brick forks between them. So, the mast gets near the trolley wire, and the wire snaps back, knocking down one side fork, shaking the wire violently, but not breaking it. So much for strummng the trolley wire like a guitar string. They only carry 600 volts DC. Rubber tires stuffed with foam handled it, so I am still hear to write about it!