Handy Welding Tips
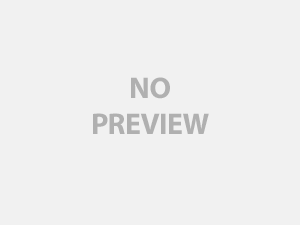
Tip #1
If you are trying to weld a thicker piece of Aluminum and you just do not have enough heat, try this trick. Switch your polarity to DC-, purchase a cylinder of Hi Pure Helium (99.997%). use 2% Tungsten, and sharpen your tungsten slightly. Your weld will come out sooty but just clean up the weld. This looks like it goes against everything you might have learned about TIG Welding, but it works just fine and will allow you to weld material much thicker than you used to!
Hardfacing
If You are Hardfacing with Tungsten Carbide for high abrasive applications, try using Vanadium Carbide instead. It cost 30% less, you get 30% more coverage per pound, and it is less likely to be damaged by the high heat of Arc Welding. The Vanadium Carbide is also deposited uniformly throughout the weld, where Tungsten Carbide tends to settle near the bottom of the weld where there is little wear!
Arc Welding
Tip #1
If you want to weld stainless steel to mild steel or high alloy steel, try using 309L-16 ($5.00 – $10.00) per pound, instead of the more expensive Super maintenance alloys
($15.00 – $30.00) per pound!
Tip #2
Always use a welding fume respirator. This could add 10 – 20 years to your life!
Tip #3
If you are using 6011 on everthing, even cleaner material, try using 7014. 7014 is stonger and runs very smooth. Also the slag almost comes off by itself!
Tip #4
To weld Cast Iron without pre heat; Keep the part cool. Never so hot that you can’t put your hand near the weld. Use stringer beads, never more than 2″ long. Then peen the weld as soon as you finish the bead.
Tip #5
If your welding rod has picked up moisture, just put it in an oven @ 400 degrees for an hour and that should bring it back to normal.
Tip #6
If your weld begins to act strange and move around on you, check to see if your welding cable is wound up, If it is, un-wind it and try welding again. If it is welding good again, you have just experienced Arc Blow. When your cable was wound up, it created a magnetic field, causing your arc to become erratic!
Oxy-Acetylene Welding
Tip #1
If you have a project that requires you to weld aluminum and you do not have a tig or mig welder,buy a pound of aluminum arc welding rod and use it to weld with your torch! This works very well,especially on thinner material.The aluminum arc welding rod is pretty expensive ($15.00-$25.00) per pound, but it does a good job and you don’t have to invest in a tig or mig welder!!!
Tip #2
If you notice your torch is starting to pop, this means that it is starving for acetylene, especially if you are using a rosebud. This usually means that your acetylene tank is almost empty. Change the tank and try your torch again. If it is still popping, the the torch has probably been damaged!!!
Tip #3
The check valve that comes standard on most torch sets sold today are designed to stop gas from backing up into your tanks through the torch. They are not designed to prevent a backflash! You must buy these separately. ($50.00–on up). They are well worth the price.
Tip #4
If you are looking for an inexpensive way to braze stainless steel with good color match-up try using nickel/silver (Harris/Welco has a thin flowing and a bead forming series-welco 14 and welco 17.).