A Taste for Guitar Building
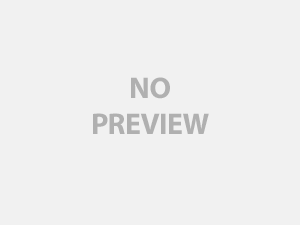
You do not need a CNC machine, laser cutter or specially trained woodworms – just a few standard tools available from any hardware store will do. A band saw and a router are essential, but if you have any doubts about using them, please seek advice about how to do so safely! Don’t beat yourself up if your first guitar isn’t up to Benedetto standards. It may take a little time to acquire all the skills and tools for complete mastery but it is possible for a complete novice to make a very playable guitar, and if you can do it once you can do it over and over again. There is always something to learn; to become a good guitar maker you will need to practice, just like anything else. It gets easier every time, but I would recommend a first time builder starts with something simple like a solid body electric guitar. Once you have done this then you could move onto other types of instrument – acoustics or archtops, maybe.
Guitar building is not very glamorous and can be quite hard work, but the end result – an instrument you have designed and built from scratch – is your reward. Oh, and be warned; you will be planning your next guitar before you have finished the first one! The best way to build your first guitar is to go on a course, but if this is not for you then there are a few things you can do to make it easier. So if you are interested in having a go yourself, here are a few tips to help you on your way:
1. Have a plan – Only a mad fool would attempt to build a guitar without a plan. Do a full size scale drawing of all your wood and parts on the back of a roll of cheap wallpaper, so you can lay them out on your drawing and check that everything fits.
2. Practice – Making and measuring patterns is a good way to acquire skills before attacking expensive timber with power tools. Use MDF or plywood for these as it is cheap and often free if you know a friendly builder or chippy (cheers Duffy!). Some handy patterns are: body shape, neck shape, pick-up hole, neck socket and control cavity.
3. Take your time – Make sure you understand the task in hand before starting each job. Always measure twice, etc…
4. To slot or not? – As the fretboard is probably the most important (and hardest) part to make, why not buy one that has been pre-radiused and slotted? There is no shame in this – and maybe if you sell your first guitar, or are making lots of them, you could invest the money in a specialist jig for fret slotting and also some radius blocks. But if you are only making the one there is really no point in going to this expense.
5. Use quality tools – This doesn’t mean you have to spend a fortune – try looking around for second hand stuff. But remember, you generally get what you pay for with new tools. Most importantly, learn how to keep them sharp.
6. Specialist tools? – You can buy one for just about every job – check out www.stewmac.com if you don’t believe me. These are fantastic time-saving devices designed to make each job easier. The cost can be high, but you could always make your own versions; I started by making all my own jigs, patterns and specialist tools.
7. Read lots of books – Try to research as many different methods of building as possible for the particular style of guitar you want to build, then you can choose the one that best suits you and the tools you have available. The internet is a great source of information; try www.mimf.com and www.LMI.com.
8. Wood – Try to buy your wood from a specialist luthiery supplier to be sure of its quality. Ask them to plane it to thickness for you, as this could save you a big headache and a lot of time. When you have received it, you will need to let it acclimatise in your wood room for at least two weeks before you start to work.
9. Hardware – Bridge, pick-ups, tuners, etc. Your parts will depend on the feel and sound you are trying to achieve. If you already own a guitar that you are really comfortable with, you could decide to go with a similar set up on the one you’re building. Novice builders are advised to keep it simple; leave a trem for the next one and keep electronic switching to a minimum.
Finally, you will need somewhere to work safely, and having seen one of our course builder’s kitchens/through lounges after having a go at home, I don’t recommend using the kitchen table (guitar building tends to take over a bit!). An important and often forgotten item is a solid surface to work on – if it wobbles it will make most jobs more difficult and results less accurate. I once made a guitar from scratch on a bit of MDF clamped to two ancient carpenter’s horses outside in the square of a medieval Italian village. I had to ask people to sit on the ends whilst I carved – so unless you have workshop assistants ready to sit at a moment’s notice, it’s probably just easier to fix your bench to a wall or the floor.
Over the years I have met hundreds of people of all ages who have successfully built at home, whatever the final result. Whether doing it as a hobby or full time, the pleasure is definitely in the building and playing that first note. Have a look at this new addict www.tonysguitars.blogspot.com and someone who has turned a hobby into a way of life www.arrowheadguitars.co.uk.
Oh, and if you find you get a REAL taste of guitar making, then you probably should have been wearing a dust mask!