Basic Issues of Beam Design
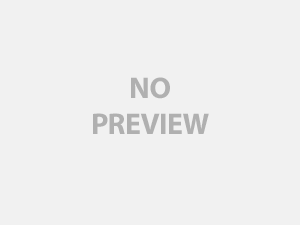
Introduction
We will now look at the basics issues involved in the design of a beam for a structure. Determining the loads on the beam (load amounts and locations) are not discussed here and for the purposes of this article may be assumed to have already been determined. Thus, once the loads for a beam are determined, we must investigate the following.
Bearing
Shear
Bending (Flexure)
Stiffness (Serviceability)
Stability
Anchorage
Proper Detailing
There are other issues not uncommonly encountered, such as dealing with notches and holes, but we will leave those for later.
Now I will elaborate on the above issues in terms of the phenomena that we want to make sure doesn’t happen, and some of the means we employ to make sure these things don’t happen.
1. Bearing
The purpose of a beam is to span across some space and carry the loads (say the weight and people and things be carried by a floor) to the supports (walls or posts) at its ends. That means that the loads can get rather concentrated at these supports. To make sure that we don’t crush (ruin) the end of the beam or the top of the supporting member we need to look at these bearing conditions. And generally what we do is calculate some minimum bearing area or length so that the force transfer can occur at these contact points without ruining something. If there isn’t enough area or bearing length available we may have to `make some more’ by adding bearing plates, or other means of spreading these loads out.
Bearing can also be an issue where we have concentrated loads coming down onto the beam, say, via a column resiting on the beam carrying loads from above.
2. Shear
Most commonly beams are used to carry `gravity’ loads – the weights of things (and the beam itself) acting downward. As we get closer and closer to the ends of a beam, the beam experiences greater and greater downward `shearing’ force internally. And this is perhaps easiest visualized near an end where we have all sorts of `weight’ the beam is carrying (maybe half the span worth), and then right at the support the upward acting reaction. This downward / upward action in the beam wants to shear or `tear’ the beam. And different materials tend to `tear’ differently.
In a concrete beam this shearing or tearing action shows up as a tendency for diagonal tension cracks to appear, at 45 degree angles to the beam axis. If there is not reinforcement in the beam, or if unreinforced but subject to excessive shear stress, the beam may break catastrophically. So in the design of concrete beams we need to make sure the stresses don’t get excessive, or if we anticipate that they might, provide proper `shear’ reinforcement.
Wood beams are typically fabricated or sawn such that the grain is parallel with the long axis (length, or span) of the beam. And whenever we have upward-downward shearing action internally, for `equilibrium’, we will also have left-right (horizontal) shearing action. So, a wood beam subject to excessive shear stress tends to split, or `de-laminate’ horizontally. Reinforcing a wood beam to resist excessive shear is less common; more often we just pick a bigger beam if we anticipate shear stresses to be excessive.
Steel (our other common building material) `shears’ differently than wood and concrete. Too much shear in a steel beam will cause it (for example the relatively thin web of the beam) to `yield’ (deform), or worse, come apart. We can, where we anticipate excessive shear stresses, reinforce steel beams for shear.
3. Bending (Flexure)
As a beam carries loads collected along it span and carries them to the supports, the beam bends, or flexes. The material on the top of the beam gets compressed, and the material on the bottom gets stretched. If the material on the bottom gets stretched excessively, the beam may break (break open – yikes!). In concrete beams the concrete along the bottom alone cannot be counted upon to resist even modest stretching (tension) and so concrete beams MUST be reinforced where they may be subject to tension action. With wood and steel, we generally make sure that there is enough wood or steel to keep the stresses low. Manufactured wood beams are generally made with higher strength wood in the tension zone, or in some cases reinforced with other materials. If the compressive stresses are excessive (let’s say in an over-reinforced concrete beam) then the material on the top of the beam may start crushing.
4. Stiffness / Serviceability (Deflection)
Okay, let’s say that we make sure the beam doesn’t shear, that it doesn’t break (open, in the middle), and that we don’t have crushing of beam or supports at the ends, or crushing in areas where the flexural compressive stresses are high. We’re still not done. Sorry, but there are still some things we need to look at. Consider a 2 x 12 piece of dimension lumber laid flat between two saw-horses. Don’t try this at home – but image now getting up on top of the 2 x 12. It probably won’t break (well, depending), but it will sag, maybe frighteningly so. And it will probably be pretty bouncy. (And make sure the saw-horses are held in place.) Now imagine beam design in general. In addition to designing beams so they don’t break, we also want to make sure the sag, or bouncy-ness, is not excessive. (Or they won’t seem safe, not matter how `strong’ we make them. The most common design task we have in this regard is to check the `deflection’ (amount of sag, typically at mid-span) of the beam under various loading conditions, and make sure that the deflection doesn’t exceed maximum values determined by the building codes or by the Architect in consideration of the needs of the Owner. Typical limits on deflection are expressed in terms of some fraction of the length. For example, a common (code) limit on the deflection due to the Live load (Occupants, for example) is length (L) divided by 360. So, the deflection under live load for a 30 ft beam (360 inches long) would be limited to 360 in. over 360 or one inch. (Let’s see if I can say this right … ) But this is a minimum maximum (deflection). We may want to, for example, limit the deflection to L/480, or L/600, or whatever is necessary for the beam to `serve’ the Owner as he/she intends (and hence the term `serviceability’). Obviously tighter and tighter deflection limitation we put on the beam, the stiffer and stiffer it will need to be, and this does not come without cost.
5. Stability
This next issue is perhaps not as obvious, but still very important. The `pushing’ on the top part of the beam (or whatever part is being compressed) also makes it want to `buckle’ (snap) to the side. For illustration purposes consider a long, slender rod that is compressed. Yeah, it buckles and snaps, sometimes under a surprisingly small (compressive) force. For a beam this buckling is a lateral-torsional buckling … with the top wanting to buckle like a column or rod but also being somewhat held in place by the bottom, which is in tension. If the beam is not braced, and this tendency is excessive, the beam may buckle in a lateral-rotational way. Instead of trying to explain it further, I provide a link to a report by the American Wood Council on the subject. It is rather technical, but does have some illustrations … (here).
In terms of `design’ the easiest way to deal with lateral torsional buckling (LTB) is to simply attach the compression zone of the beam to something to keep it from buckling (moving laterally). This is commonly accomplished in, say, simple spanning floor beams, by deliberate attachment of the floor to the top of the beam. (Yes!) If the beam is not adequately braced, then we need to make to also check its `capacity’ with regard to buckling. Common design practice is to reduce it’s bending (flexural) capacity as needed to also accommodate potential buckling.
6. Anchorage
Less discussed (it seems) in beam design, but still very important, is the issue of anchorage. We need to make sure all of our beams are anchored in place, say, against some earth shaking, or something else tending to yank it off the supports. For example, beams must be at least positively attached (by bolts, welds, metal clips, whatever viable means …) to resist a force parallel to the beam that is generally some percentage of the design `gravity’ load on the beam. In my immediate area of practice I have used values ranging from twelve to fifteen percent of the total design Live and Dead load. But in an area of greater seismic risk or activity this percentage would be greater, maybe way greater. We do NOT want a beam coming off a support, along with everything supported by the beam.
7. Proper Detailing
Proper detailing is another issue that is not necessarily talked about much, but is still very important. As engineers we specify a lot of beams (sizes, materials, grade of materials, etc.) but we may be fairly silent with regard to the proper framing details (and this may be good or bad). On the one hand, maybe we are leaving the `detailing’ up the the Contractor … assuming he/she/it will make sure that the beam is installed properly … or, on the other, we may generate very specific drawings and details as to how it goes in place, is attached, etc. Beams, for example, must be `held in place’ at their ends so that they don’t roll (flop) over. They must bear on enough of the supports to satisfy the minimum bearing area or lengths required. Additional bracing may be required. We may also need to detail connection points so that moisture doesn’t get trapped, and / or so things can expand and contract a little (or a lot), or rotate, if needed. Some detailing issues are spelled out in the Code; some must be spelled out by the Designer; and some are left up to the Contractor; and the `amount’ of each one of these `somes’ may vary from project to project, type of construction to type of construction, and even the particular contractor. As such, at least some of proper detailing is an art … how much to show, or specify, and to whom.
Conclusion
Above are the main issues of beam design. There are other things we have not covered, such as, “what about holes, notches, tapers in beams?” There are other stability issues, like `ponding’ on flat or near flat roofs. But we have covered enough for now.
References
American Forest & Paper Association / American Wood Council, 1111 Nineteenth St., NW, Suite 800, Washington, D.C., 20036, www.awc.org.