Building Your Own Cabinet Doors: Part 2
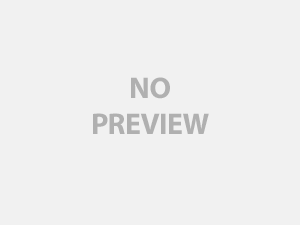
With your cut list in hand move on over to your table saw. You will need your miter gauge for the cross cuts. Remember do not use the table saw rip fence for making cross cuts on solid wood. You will likely experience a kick back and could be seriously injured. Alternatively you could make these cuts with a miter saw set for 90 degree cuts.
Mark the lengths of your pieces as indicated on the cut list you made earlier. Then carefully cut the 2″ wide stock to length. Be sure that your cuts are square to the length of the board to make a nice joint without gaps later. By the way if you are going to buy a table saw for this job, I suggest the Rigid TS3650 table saw. It is an afford-ably priced table saw that can accommodate most cabinet making tasks. I bought mine about 2 years ago for less than $600.
Once your cuts are made, separate your frame pieces into horizontal and vertical pieces. You will want to start at the router table with the horizontal frame pieces.
It is important that you use a router table when using larger router bits. The larger router bits are just too much to handle safely with out the table. Good router tables can be purchased from Rockler.com, mlcswoodworking.com and other woodworking suppliers. I built my own router table to fit my needs and so can you. There are several plans available for free and for purchase on the Internet. My only suggestion is to buy a table with a large surface. You will end up using the router table for more and more projects as you learn to use it. It is also advisable to purchase a coping sled from one of the woodworking suppliers. A coping sled makes cutting this joint safer and makes a much nicer joint than trying to free hand it.
Start with the coping bit in your router. You will need a router with 1 �½ HP at a minimum, best to use a 2 HP router to spin this large bit. I use Dewalt routers; they are affordable and take daily use very well. When you are selecting your cope and stick router bits, try to find ones that have optional set up blocks available. This will make setting up your router easy and ensure that your joints fit like they should.
With the coping bit in the router and the router mounted to the table, you can begin making your cope joint cuts. These cuts will be made in the ends of the horizontal frame pieces. When you are finished with this operation you can move on to the stick cuts.
Again with the router mounted to the router table, chuck your stick cutting joint bit in the router. Use the set up block to carefully set up your cuts. It is advisable to make a test cut in a scrap piece of wood to check your set up, adjust as needed. If your test cut shows a good set up, you can cut the stick joints in one edge of each of the horizontal and vertical frame pieces. Use push blocks to feed the wood through the bit to keep your hands clear of the bit. The bit is very sharp and spinning very fast. You can be seriously injured if you are not careful.
Congratulations you have made your joinery cuts safely, that was fun. Now test fit all of your pieces. Don’t worry if they don’t come quite together at this point, the pieces are probably a bit fuzzy from the cutting. With some sanding and clamps they should come together nicely if you have been accurate in your set ups and cutting. Dry fit the parts and measure to make sure your doors will be the correct size.
With that done we need to do just a little more math. I know I said earlier that the math was done but I forgot about cutting the panels that will fit inside the frames. We will assume that your router bits cut 3/8″ grooves and tongues, most do for cabinet doors. This will be pretty easy math. Part of it is already figured out. The width of the panels you will need to cut is the same as the length of the horizontal frame pieces. We only need to calculate the length of the panels.
We will use the overall height of the door as our starting point to calculate the length of your panel. Using our example of the 19 Ã?¾” door heights we will subtract 4″ for the width of the horizontal frame pieces and then add Ã?¾” for the two 3/8″ grooves. So our math is as follows: 19 Ã?¾” – 4″ + Ã?¾” = 16 Ã?½”. So your panels for the example doors will be 11 5/8″ wide by 16 Ã?½” long and 14 Ã?¼” wide by 16 Ã?½” long.
Cut your panels from the Ã?¼” oak plywood at the table saw. You will likely need help from another person if you purchased a 4′ x 8′ sheet of plywood.
Take all of the pieces you have just cut to your work bench and sand all the surfaces smooth. Be careful sanding the plywood as the oak veneer is very thin. I like to use a random orbit sander with a 120 grit sanding disc for the plywood faces. Use a piece of 100 grit sandpaper wrapped around a block for the plywood edges to smooth. For the frame pieces start with 80 grit paper on the random orbit sander or sanding block to smooth all the cutting marks. Progress to 100 grit and 150 grit sandpaper.
Wipe the surfaces clean of the sanding dust and get out your stain. If you will be applying a stain now is the time to stain the panels. If you assemble the doors first and then stain the panels, you may find that with seasonal movement of the wood that small areas of the panels will show without stain. It is only necessary to stain the front face of the plywood panels. Allow the stain time to dry as recommended in the instructions.
Now that the stain is dry you can assemble the doors. Start by collecting your pipe or bar clamps and setting them up to accept the width of the door. Apply a small amount of glue to the coped ends of the horizontal pieces. It is not advisable to apply glue to the grooves that will hold the panel in place. The panels should be allowed to float free in the frame to allow for seasonal wood movement.
On a flat surface such as your workbench, assemble the two vertical frame pieces to one of the horizontal pieces. Clamp with slight pressure just to hold the three pieces together and then slide the plywood panel into place. Apply glue to the cope joint of another horizontal frame piece and finish assembly of the door. Apply clamps to the joints and tighten just enough to hold the pieces together. Use a dead blow hammer to adjust the horizontal frame pieces so that they are flush at the outside corners with the verticals. Tighten the clamps slightly more and set aside. Do not over tighten the clamps, this will likely cause the door to warp. It does not take much pressure to hold the joints together long enough for the glue to dry.
Depending on the temperature and humidity of your shop you should be able to remove the clamps in an hour or so and safely continue working on the doors. We are almost finished here and I am sure you are excited to see just how nicely your doors have come together.
Once again sand the frame pieces with 100 grit then with 150 grit sandpaper to smooth the surfaces. You may wish at this time to route a decorative edge on the outside edges of the doors. I like to route either a 3/8″ round over or 3/8″ cove around the outside edge. At least ease the sharp edges of the doors with sandpaper if you do not wish to have a decorative edge.
Wipe away the sanding dust and finish staining the fronts and backs of the doors. Once the stain has dried I prefer to use a satin finish clear coat polyurethane. I normally buy polyurethane in the spray can and apply 5 or 6 thin coats. Allow each coat to dry before proceeding to the next coat.
All that is left is selecting hinges and pulls and installing them. There you have it, your finished cabinet doors. Stand back and admire your work and be proud. Don’t forget to see Part 3 of this series which is a short video titled; “Building Your Own Cabinet Doors: A Video Presentation”.