Deconstruction as an Alternative to Demolition
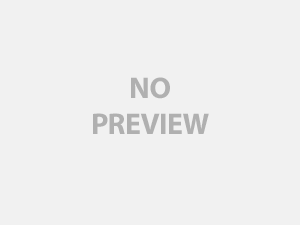
Deconstruction is the process of taking a building or structure apart, selectively dismantling and removing materials before the structure is demolished, or avoiding demolition altogether, and disassembling the entire structure, in the reverse order in which it was constructed. In some cases deconstruction can be a complement to demolition, replacing certain elements of demolition and providing the opportunity to enter a building and remove materials that can be salvaged and reused.
The demolition of building structures generates millions of tons of material each year, most of which ends up as waste in landfills. According to different sources, the demolition of buildings can produce upwards of 125 million tons of debris each year. The U.S. Environmental Protection Agency’s estimate is 136 million tons, with only 20-30% of that waste being recycled. In terms of the number of building, according to estimates there are about 245,000 residential structures and 44,000 commercial structures that are demolished each year.
Deconstruction provides an environmentally preferable way to remove a building, salvaging materials and reducing energy consumption, while at the same time generating more jobs, and saving resources. This is a process that has existed throughout history, but that is taking on more relevance today.
Helping the Environment
Salvaging materials through deconstruction helps reduce the burden on landfills, which are already at capacity in many localities. Landfills can cause a number of environmental hazards for the local community, including air-borne toxins, ground water pollution, and the risks caused by the improper disposal of wastes. Deconstruction can lessen the burden on existing landfills, and reduces the need for additional landfill space. It can also reduce the emission of gases by reusing or recycling materials that would otherwise be incinerated.
By focusing on the reuse and recycling of existing materials, deconstruction preserves the invested energy already embodied in materials, eliminating the need to expend additional energy to process new materials. And, by reducing the use of new materials, deconstruction also helps reduce the environmental effects, such as air, water and ground pollution resulting from the processes of extracting and processing the raw materials needed to produce those new construction materials. Many mineral extracting operations that produce the raw materials used in construction, use cyanide or sulfuric acid leaching processes. These chemicals can seep into, and contaminate groundwater reserves. The production of polyvinyl chloride (PVC), a commonly used construction material, releases airborne dioxins. Reducing the need for additional new raw materials by using deconstruction techniques, can reduce these sources of pollution.
Deconstruction results in much less damage to the local site, including the soil and vegetation, and generates less dust and noise than demolition. And, deconstruction can also contribute to turning around the pattern of consumption and disposal, and move more toward a pattern of reuse and sustainability.
Creating Jobs and Helping the Community
Deconstruction is a labor-intensive process, involving a significant amount of manual work, removing materials that can be salvaged, taking apart buildings, and preparing, sorting, and hauling the salvaged materials. This can create jobs, especially for under-skilled and unemployed workers.
In many urban revitalization projects, where there may be more building removal work that can lend itself to deconstruction, there could also be a large pool of unemployed workers available. Deconstruction can provide them with the opportunity to gain skills, and thereby generates a new source of employment opportunities.
Deconstruction can serve as a training ground for these workers. Skill levels in the local labor pool can be improved by teaching jobsite safety, the use of tools, and construction sequencing, while actually deconstructing a building. By showing workers how to take buildings apart, they will be much better prepared to enter the construction workforce with the necessary skills, meeting the demand for skilled and experienced workers in the construction industry. Industry training costs are reduced, and new employees can become income generators.
Deconstruction is increasingly in demand in government projects, as governmental entities are under pressure to reduce wastes. The Department of Defense promotes deconstruction rather than demolition of military bases. Having the capacity to carry out deconstruction projects can therefore open up new business opportunities for construction and demolition companies. These companies may have access to contract bidding that would otherwise not be available to them. There are millions of dollars in federal funding available for public housing and urban revitalization projects. Deconstruction can also stimulate the development of small businesses to handle the salvaged materials from deconstruction projects, for resale and reuse, or recycling.
Deconstruction also supports and complements other community initiatives, such as providing materials for housing programs. By providing affordable, readily available materials, deconstruction can help to alleviate housing shortages or substandard housing in the community.
Saving Resources
Deconstruction provides a source of durable, often high-quality, affordable building materials. The materials removed through a deconstruction process can be reused in new construction, and for remodeling and landscaping projects. Or, the recovered materials can be sold to a salvaging company. The market value for salvaged materials from deconstruction is greater than from demolition due to the care that is taken in removing the materials in a deconstruction process.
By deconstructing, some of the investment in the original structure can be recovered, rather than being totally lost, including the energy cost invested in producing the original materials. By deconstructing, this energy cost can be saved, and the use of additional energy to reproduce those same materials can be avoided.
Cost of Deconstruction
Deconstruction, as an environmentally-sound business practice, is not necessarily more costly than traditional demolition. Buildings can be often be deconstructed more cost-efficiently than they can be demolished. There are many different factors involved, including the type of construction and the value of the materials that can be recovered. But overall, deconstruction can be more cost-effective than demolition. Preliminary results from pilot projects carried out in different parts of the country have indicated that deconstruction may cost 30 to 50% less than demolition.
Deconstruction is labor-intensive, involving a higher level of manual work than there would be in a demolition project. But the higher labor cost can be offset by lower costs for equipment rent and energy usage, cost savings in the form of lower transportation and landfill tipping charges, and the revenues from sales of the salvaged material.
Materials That Can Be Salvaged
Materials salvaged in a deconstruction project can be reused, remanufactured (processed for a different use), or recycled (turning damaged wood into mulch, or cement into aggregate for new foundations or sidewalks).
Depending on the building, when and how it was constructed, there may be valuable components that can be recovered. One of these is the timber, or lumber used in older buildings. The disassembly of wood-framed buildings was once quite common in the United States, when the cost of labor was low, the cost of materials was high, and heavy equipment was not as common as it is today. But today, as deconstruction is taking on new importance for environmental and sustainable development purposes, there is also a growing realization that high quality “old-growth harvest” lumber can be salvaged. This lumber often has a higher aesthetic value, due to its higher density, slower growth, and fewer defects than a lot of the lumber produced today, and there are many people who are willing to pay for this quality. Good quality lumber can carry a high price in the specialty building products market.
Certain types of buildings may have features that have an intrinsic value, such as architectural and ornamental antiques. These could include antique appliances, kitchen and bathroom fixtures, cabinets, trim work, and floor tiles. Wood flooring, raised panel doors, ornate interior and exterior trim, electrical and plumbing fixtures, framing, and bricks, can have a salvage value of up to 75% of their original value.
Other materials that can typically be recovered include windows, cabinetry, sinks, countertops, mirrors, light fixtures, carpeting, baseboards, floorboards, stair treads, roof joists, carpeting, ducting, fencing, insulation, plumbing, wiring, and landscaping materials. Clay bricks, roof tiles, clay and stone paving, and stone walling can also be reclaimed. Depending on their condition, roofing materials such as concrete or clay tiles, slate, copper, vents and flashing, and sheet metal may be salvageable.
Metals recovered through deconstruction are good candidates for recycling, since even if they are bent or torn apart, they still retain a relatively high value. Lumber, on the other hand is better suited to reuse. Possible end uses for lumber that is torn apart include chipping, for mulch, fuel, or possibly for particle board or fiberboard. But these uses have a lower value than lumber that is salvaged intact, and that can be reused.
Tax Deduction
Another way deconstruction can potentially reduce costs is through a tax deduction for the donation of salvaged materials. A tax deduction can be taken for the fair market value of materials donated to a recycling organization that participates in deconstruction, provided the organization is recognized by the IRS. A 501(c)(3) corporation qualifies for tax deductions, and the tax benefit can help to offset the cost of deconstruction. To find out whether a certain organization is a qualified charitable organization for tax purposes, you can check Internal Revenue Service (IRS) Publication 78. There is a search facility for Publication 78 on the IRS website, that enables you to look up charitable organizations by name.
Options for Deconstruction Contracts and Costs/Revenue Splits
There are different business models under which a deconstruction project can be carried out. The following are examples:
1. The building owner pays a contractor for the deconstruction service and retains ownership of the salvaged materials. The owner may pay more than a demolition would cost, but could be “buying back” high value materials.
2. A contractor performs the deconstruction service with shared ownership of the materials. The contract price may be reduced based on the contractor receiving materials as a partial payment in-kind.
3. The contractor performs the deconstruction and retains all materials, with the contract price based on revenues to be received from the resale of the salvaged materials.
4. A non-profit contractor does the deconstruction for a fee, and the owner takes a tax deduction for the value of the donated materials.
Challenges
Even though there are significant advantages to deconstruction as a option for building removal, there are certain challenges faced by this alternative:
�· Existing buildings and their components are not necessarily designed for disassembly and deconstruction. Plywood and composite boards are difficult to remove, and new building techniques, including gluing floorboards and using high-tech fasteners, inhibit deconstruction.
�· Deconstruction requires additional time. Time constraints and financial pressure to clear the site quickly, due to lost time resulting from delays in getting a demolition, or removal permit, may detract from the viability of deconstruction as a business alternative.
�· Deconstruction is a labor-intensive effort, using standard hand tools in the majority of cases. Specialized tools designed for deconstructing buildings often do not exist.
�· The proper removal of asbestos-containing materials and lead-based paints, often encountered in older buildings that are candidates for deconstruction, requires special training, handling, and equipment.
�· Re-certification of used materials is not always possible, and building codes often do not address the reuse of building components.
�· There are limits on potential demand for salvaged materials, due to lack of awareness of their availability, lack of awareness of the significant price differences between salvaged materials and new materials, not being able to find salvaged materials when they are needed, or not finding enough of them to complete a project, lack of awareness of the environmental benefits of using salvaged materials, and the perception that salvaged materials are inferior in quality.
The Road Ahead
Historically, provisions have not been made for the future disassembly of buildings. They were generally built to be permanent. But deconstruction is emerging as an alternative to demolition around the world, with significant backing by government and non-profit organizations. Techniques and tools for deconstructing existing structures are under development. Government policy is beginning to address the advantages of deconstruction, and disposal costs are being increased for material that could be reused. Designing buildings to facilitate future deconstruction is receiving more attention, with studies being performed and information exchanged between research organizations and practitioners around the world.
In many different municipalities, actions have been taken in favor of deconstruction, by incorporating “green” provisions into their building permit granting process. For example, The City of Boulder, Colorado has a “Green Points Building Program”, whose purpose is to:
Ã?· Help owners find materials and designs for building “green”,
�· Encourage homeowners to use cost-effective and sustainable remodeling and building methods that conserve fossil fuels, water, and other natural resources, and
�· Promote the recycling of building materials and reduce sold waste.
The program requires applicants to earn “green points” in order to get building permits. A certain number of points are required for new construction, interior remodeling, and additions. Points are earned by using a deconstruction plan instead of demolition, using recycled materials in the construction, and using building and landscaping plans that reduce land and water use. The City of Austin, Texas has a similar green building permit program.
The Center for Construction and Environment at the University of Florida has carried out a research project to assess the economics and techniques of deconstruction. A similar deconstruction pilot project was performed at the Mather Air Force Base housing site in California. The Integrated Waste Management Board of California works with contractors, builders, engineers, architects, and local governments to encourage the use of deconstruction.
The Institute for Local Self-Reliance, a non-profit organization with offices in Minneapolis, Minnesota and Washington D.C., is working with the U.S. Department of Housing and Urban Development (HUD) to see how deconstruction can be used to help meet public housing goals. And, the U.S. Forest Products Laboratory is doing research to re-grade lumber extracted from buildings, in order to re-certify it for use in new construction.
Designing for Deconstruction (DfD) is an emerging concept that considers the whole life cycle of a building, from initial design through eventual removal, incorporating aspects of disassembly, recycling, and reverse manufacturing.
Sources Near You
ReStore, associated with Habitat for Humanity, has a national chain of used building materials stores, where prices for salvaged dimensional lumber are typically set at 50% of retail prices for new lumber. Prices for salvaged timber vary, depending on their quality, size, and species. Remanufacturing can significantly increase the lumber’s value, especially for use in flooring, where certain characteristics of salvaged lumber, such as nail holes and discoloration, can actually be quality attributes for buyers looking for more of a rustic, or antique appeal.
The Building Materials Reuse Association’s website (www.ubma.org) has a directory of deconstruction contractors and suppliers of reusable building materials.
The Forest Products Laboratory of the U.S. Department of Agriculture, in cooperation with the Powell Center for Construction and Environment of the University of Florida , has published a directory of companies and organizations involved in wood-framed deconstruction, dismantling, and reused building materials, with an emphasis on those that use, resell, or remanufacture salvaged wood. The directory, entitled “Directory of Wood-Framed Building Deconstruction and Reused Building Materials Companies” includes a listing by state and by type of activity, and can be found on the Internet at www.fpl.fs.fed.us.
Others are Reading
Posted by john in Decorating & Design