Design of Concrete Basement Walls
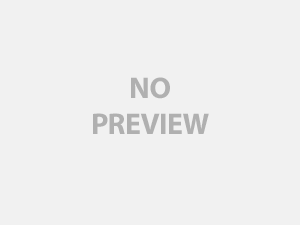
Outline
- Introduction
- How Basement Walls Act
- Vertical Spanning One-Way Walls
- Horizontally Spanning Two-Way Walls
- Cantilever Walls
- Concluding Remarks
- References
1. Introduction
By a basement wall I mean a wall with living space on one side and outside soil or other backfill on the other, and a superstructure overhead. And, it is made of concrete, reinforced concrete. No doubt there are many concrete basement walls without reinforcement. I own a home with some cracked plain concrete basement walls, and they are cracked, way cracked.
With regard to supporting the superstructure above, concrete basement walls are strong. Unless they are severely out of plumb, they carry the loads from above in compression – and concrete `is doing its thing’ in compression. But when we have a tall concrete (basement wall), with `air’ on one side and soil (pushing) on the other, we are also loading the wall laterally, or transversely, causing it to bend, putting some concrete in tension. Concrete is weak in tension, so we add reinforcement. No doubt the vertical load from above helps negate some of this tension, but since these loads may be light (the wall isn’t a major bearing wall), and they vary as we go along the perimeter of the building, we (or at least I) don’t count the benefit of the axial compression in the wall. So, we are gonna add use reinforcement. Besides, around here I (where I practice) I have not seen a plain concrete basement wall get past the building officials.
Concrete basement walls have been cast for decades between plywood (or other) forms leaving a solid core `flat face’ wall. The forms are removed once the concrete is hard, and then used as forms for subsequent walls, or in some cases as the floor sheathing as construction progresses. (Hey, I’m simply reporting what I have seen, whether or not I recommend it.) More recently Insulated Concrete Form (ICF) systems have become popular, where the forming system remains in place after construction to provide insulation and (ideally) various means to accommodate wall finishes and even more ideally electrical runs, etc. For the purpose of this discussion the ICF systems are simply another forming system for a basement wall AS LONG AS THEY RESULT IN A SOLID-CORE FLAT FACE CONCRETE WALL. (Some ICF systems don’t; but I will not get into that here.)
2. How Basement Walls Act
Intended or otherwise, basement walls act to resist the earth pushing in (lateral earth pressure) three main ways.
- Wall Spanning Vertically from Floor to Floor
- Wall Spanning Horizontally from Return or Buttress to Return or Buttress
- As a Cantilever
In reality most walls end up actually acting in some combination of the above. For example, a wall that spans horizontally from return to return will be attached to a footing and/or bear against a basement slab at its bottom and may also be attached to a floor at its top. And so to some extent is will also span up and down (intended or otherwise). Walls that intended to span both directions behave as `two-way’ slabs. And it is the `two-way slab’ situation that I will cover in more detail as I cover `way’ number 2 above.
3. Vertically Spanning (One Way) Walls
Vertical spanning walls are pretty simple structurally. They flex inward between the floors at top and bottom with the concrete in tension on the living side. Hence, reinforcement is often placed toward the inside (inboard face). They may be designed prescriptively (Rx Basement Walls … here), or by calculation (by an Engineer, … here). Tall basement walls, or walls supporting structures that are outside the limitations of the prescriptive design path require calculations. An ICF wall of slightly unusual width (hence needing to be calculated) is covered in the link above (linked again here). One advantage of the vertical spanning wall is that it may be really long (in some sense unlimited). Several disadvantages are: 1) there MUST be a floor attached to the top of the wall; 2) such attachment is quite robust (lots of anchor bolts, etc.). And let me state the first disadvantage another way: it won’t work if there is a significant opening in the floor next to the wall, such as a flight of stairs, or where some room is `open to above’.
4. Horizontally Spanning Two-Way Walls
Two-way walls span from return to return, and also somewhat vertically. They may or may not `count on’ the floor at the top for support. By `return’ I mean where the wall `turns a corner’, for example, at a corner of the structure, or where the wall bumps out (or in). Presently there are not prescriptive provisions in the International Building Code or International Residential Code for such walls, however, some local jurisdictions may have provisions for such basement wall types, though they may not be named such. They are recognized by limitations and requirements that end up being pretty similar to the guidelines I end up providing below.
The actual structural design of two way systems is more complicated than one-way (simple) spanning systems. I generally us the tabulated results of a report by the Portland Cement Association on “Rectangular Concrete Tanks” (See reference at end). (Don’t laugh; there isn’t much out there on basement wall `engineered’ design … and that’s what I have found other engineers using for basement walls as well.) Or, I solve the wall using a Finite Element (computer) Analysis (FEA).
It is important to note in two-way wall systems that the zones of concrete in tension are in some places on the inside of the wall and in others on the outside. Between the returns (and between the floors above and below) the tension zone of the concrete is on the inside. Nearing and going around the corners, however (the `returns’) the concrete is in tension on the outside (soil side). What this means is that if the reinforcement is to be used as efficiently as possible then it must be in some areas near the `inboard’ face and in others more `outboard’. Big, thick (thicker than 10 in. thick), tall, heavily loaded walls will require two mats of reinforcement anyway (one inboard and one outboard), so this is not necessarily a big deal; however, for residential construction only one layer (mat) of reinforcement. As such, I generally detail a single layer of reinforcement at or near the center of the wall and then either detail the reinforcement necessary to resist the lateral earth pressure loads, or I prescribe maximum return distances to accommodate a chosen reinforcement schedule. Where returns are not available (long runs of walls), then buttress walls or counter-fort walls are necessary.
Two Way Basement Wall Recommendations
So, here is the approach I take for two-way basement walls.
- I do not count on the floor at the top of the wall for providing support. In that way a floor at the top of the wall is not necessary. In fact, the particulars of a project in question may dictate the absence of a floor at the top and necessitate a two way (or cantilever system). Plus, I don’t have to design the connection to a floor (that is not required to exist).
- I consider a basement wall a `wall’ according to the ACI code. As such, I always specify minimum `wall’ amounts of reinforcement (ACI 318 Chapter 14).
- I detail the reinforcement in the center of the wall, to make construction simpler, and also eliminate the possibility of reinforcement ending up nearer the `wrong’ face.
- I work with the Architect (or Owner) in coming up with a plan to provide the necessary returns or buttress (or counter-fort) walls, or,
- I detail additional reinforcement (or execute different design approaches) as necessary for longer wall runs.
And having done such on numerous projects, I have come up with the following generic recommendations for two-way basement wall systems.
Recommended Maximum Distance Between Returns
ACI min. reinforcement., Gr. 60 (ACI 318 Sec. 14.3) centered in wall
8 in. Thick Wall, 8 ft Max Height:
Design Lateral Pressure … Max Distance
30 pcf … 18 ft
50 pcf … 13 ft
10 in. Thick Wall, 9 ft Max Height:
Design Lateral Soil Pressure … Max Distance
30 pcf … 21 ft
50 pcf … 16 ft
Prescriptive At Rest earth pressures are provided in the Code (e.g., IBC Table 1610.1) per backfill soil type. Generally reinforced concrete systems are considered `rigid’ and thus should be designed to resist `At Rest’ pressures. However, the code allows walls not extending more than 8 ft below grade and supported by a flexible floor system (at top) to be design with Active pressures. Active pressures are less and assume some movement of the wall. In this regard I interpret `no’ floor at the top to be a flexible one (for a two way system).
Examples showing the minimum amounts of reinforcement and calculations translating the minimum amounts to bar size and spacing are in another lesson (here, Sections 5 and 6).
For an 8-in. thick wall with 60,000 psi specified yield strength for the reinforcement, and using # 4 size bar, the ACI minimum values translate to: # 4 @ 12 in. o.c. horizontal and # 4 @ 16 in. o.c. vertical.
For a 10-in. Wall … # 5 @ 15 in. o.c. each way would work.
Notes: 1) in no case do I specify reinforcement spacing greater than 18 in. o.c. (it’s an ACI `wall’, remember, and 18 in. o.c. is the ACI max spacing of reinforcement (of any size) in a wall); 2) though it’s a bit counter-intuitive, thicker walls require more reinforcement since minimum reinforcement amounts are generally given in terms of ratios (steel area to concrete area); and 3) horizontal reinforcement must continue around corners and across buttresses or counter-forts to achieve the proper two-way action. This will require proper splicing, which I cover in the lesson on `Bond’, Part 2 (here).
In all cases I generally require that the returns extend at least 6 ft full height. In long, straight basement walls I work with the Owner / Architect to integrate buttress walls into planned interior basement walls.
Buttresses generally require robust footings, and so do counterforts.
5. Cantilever Walls
Cantilever walls are rare for basement use. They are characterized in general by large footings and a lot of rebar. Such walls act like vertical cantilever beams. The tension face of the concrete is on the soil side and as such that’s where we’ll expect to see the rebar. Large footings are required for stability so the whole wall and footing system doesn’t tip into the basement. These are kind of a `last resort’ design approach for basements but are common for other applications (roads, etc.). Structurally they can be essentially unlimited in length as long as accommodation for expansion/contraction/shrinkage is provided.
If used as a basement wall, and if the top is attached to a floor (or other) system, consider detailing the reinforcement closer to center of the wall (and more of it) as the floor may resist movement of the top of the wall and tend to reverse the anticipated moment.
6. Concluding Remarks
So, there are some ways to tackle basement walls. All the designs mentioned above require lateral support at the bottom of the wall, typically provided by pouring the basement slab concrete directly against the bottom face of the basement wall, and providing `enough basement slab’ so that the bottom of the wall can’t push in.
Basement walls are constructed every day, but there has really not been much design information available, with the exception of the more recent one-way prescriptive stuff. A lot of walls have been built that were not properly design, or not designed at all. And a lot have broke. Many have broken and owners have just had to `live with it’. Some get fixed, but foundation fixes are costly. Others have broken and haven’t been discovered yet. Others haven’t broken yet, and may never. The big killer of basement retaining walls is water. Backfill against the wall that is not properly drained may end up exerting pressures way greater than those accounted for in even the more conservative (`robust’) designs. And the other big killer of retaining walls, as with all foundations, is poor bearing soil. No amount of reinforcement can save a wall from cracking or breaking due to being placed on unacceptable soils. “Don’t build on fill!”
7. References
Residential Foundation Details by Calculation, Associated Content.
Building Code Requirements for Structural Concrete, ACI 318, American Concrete Institute, P.O. Box 9094, Farmington hills, Michigan, 48333.
International Building Code, International Code Council, 4051 West Flossmoor Road, Country Club Hills, IL 60478.
International Residential Code, International Code Council, 4051 West Flossmoor Road, Country Club Hills, IL 60478.
“Rectangular Concrete Tanks,” by Javeed Munshi, Portland Cement Association, 5420 Old Orchard Road, Skokie, Illinois 60077.