Differences Between Modular, Manufactured, Panelized, and Precut Homes
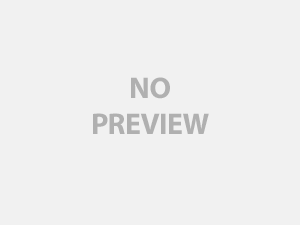
Often when people think of factory built homes, they think of mobile, or manufactured homes. The term mobile home is no longer used because of regulations that were put into place during the seventies by the United States Department of Housing and Urban Development (HUD). Manufactured homes are built to the federal building code that HUD administers. Depending on the size, a manufactured home can in one or more parts. Normally shaped like large rectangles, a manufactured home is easy to identify.
Once a manufactured home appears on site, there is usually very little work to be completed. Manufactured homes often come with most systems already completed and much of the cosmetic work, such as paint and flooring. They have siding or some type of exterior finish already applied.
Overtime, the value of a manufactured home depreciates, or loses value. Manufactured homes also have finite expectancy of usefulness. Most manufactured homes are replaced within twenty years with some other type of construction or a newer model.
Modular homes are often confused with manufactured homes, but there are some very important differences. Modular homes are built in pieces, but they have no standard shape. Each modular home is composed of two or more modules. These modules arrive on site and must be assembled and finished by a licensed contractor. A foundation and site work must be completed prior to delivery. Modular homes increase in value over time, just like on site construction.
Modular homes come without most of the exterior work and interior work completed. They are built to meet or exceed state and local codes. Because modular homes are built to be transported around the country, they are often constructed better than homes built on site. The construction techniques used ensure a home that has less heat loss, saving you energy and therefore money over time.
Panelized homes come shipped flat from a factory. A construction crew is required to assemble the pieces, but each piece contains the pieces needed for the wall. This includes wiring, windows, doors, and exterior siding. Panelized homes are required to meet both the state and local building codes that oversee the area where they are constructed. The major advantage of buying a panelized home is the overall savings in construction time and labor costs.
A precut home is like a kit for making the exterior of a house. You may be familiar with log homes as an example of this type of factory built home. Other factory built homes that fall under this category include kit or dome homes. A precut home is subject to the state and local codes where it is built; therefore it does not depreciate in value.
Precut homes often only include the exterior of the home in the price. You must be willing to hire a contractor to add plumbing, electrical, and interior considerations. This includes interior walls, flooring, and major items such as sinks and showers. Kit homes offer the least amount of materials required to build your home, so the cost to finish your home can easily triple the total cost of the home.
Weigh carefully both the long term and short term costs of these varying types of factory built construction. You may initially save money with a manufactured home, just to find that your money would have better been spent investing in a modular or kit home. Conversely, if you are not interested in building worth using your home, a manufactured home may be an excellent option to save money on rent over time. The best decision when choosing a home will take into account both immediate and later needs.