Engineering Analysis of a Hole in the Side of a Glulam Beam
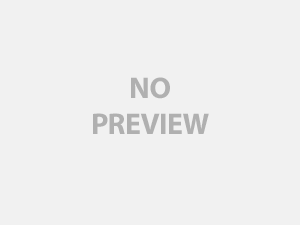
In an earlier article we investigated whether or not two holes were permissible though the sides of a glued laminated timber (glulam) beam. The holes were not particularly large, one being 2 inches (in.) in diameter, and the other 1 in. in diameter. The investigation asked, in particular, whether or not the holes were permissible `without engineering analysis’. And in that investigation we found that one was (permissible), and the other not. In this article we will investigate whether or not the hole that was not permissible without engineering analysis, is, perhaps, with.
As a basis for the former investigation, and this one, we use the American Institute of Timber Construction (AITC) Technical Note 19, Guidelines for Evaluation of Holes and Notches in Glued Laminated Tiber Beams, 2012. The Technical Note is valuable to both engineers and non-engineers in that it provides criteria for permissibility that can be handled without the expertise (and certification) of a professional engineer, and, if need be, the tools for those situations requiring engineering analysis. In this article we will `further analyze’ the hole that wasn’t permissible without analysis. In the strictest sense, then, this article will provides an example analysis intended to be carried out by engineers. In some instances, however, such calculations might be accepted by a Building Official, without engineering certification, provided they are demonstrated to follow a rational calculation path. The Building Official has the final say. Some building officials require engineering certification `for everything’; some may accept rational (engineering) calculations without certification; and some require both (certification and supporting `calcs’.) Here goes …
The beam being considered is a 5-1/8 in. wide by 15 in. deep glulam beam that spans 20 feet (ft). The 2 in. diameter hole proposed is to be 10 in. from the top and 2 ft from one end. The other hole is one 1 in. in diameter, at the mid-depth, and 6 ft from the same end. The 2 in. hole was found not permissible without further analysis; the 1 in. hole was found okay. Now let’s look closer at the 2 in. hole. We will use Pages 2 through 4 of the AITC Tech Note. In our earlier analysis the actual forces and stresses on and in the beam were not considered. It was presumed, if any thought to capacity was given at all, that the beam was adequate as is (no holes). To do an engineering evaluation of the holes we need to also know the design loads on the beam, as well as the Design values (Allowable stresses). In essence we will be seeing if excess capacities of the beam at the hole locations accommodate the losses in beam capacities due to the holes.
From Page 2 of the Tech Note, let’s first look at the general limitations of larger holes.
“1. Concentrated loads at location of holes should be avoided.”
We assume that the applied loads on the beam are `uniform’, though, in reality, they likely arrive via joists or other framing members. Such loads will be, technically, concentrated, but, we will assume, not large. (In other words, we assume there are no large `column’-type loads at the hole location.)
“2. Holes must be circular or rectangular with rounded corners.”
Our hole is round; good.
“3. The distance from the nearest edge of the of the hole to the face of the nearest support … must be greater than or equal to half the beam depth.”
Our hole is 24 in. – 2 in./2 = 23 in. from the end of the span, and the beam depth is 15 in., so we are okay (23 versus 15/2 = 7.5).
“4. The distance from the nearest edge of the hole to the end of the beam … must be greater than or equal to the beam depth.”
The beam spans 20 ft and is at least that long, depending on the details of the end connection. So, 23 in. versus 15 in.; good!
“5. Rectangular holes …”
Not applicable.
“6. The hole dimension measured perpendicular to the longitudinal axis of the beam … must be less than half the beam depth … or 14 in.”
Our hole is 2 in.; good.
“7. The distance from the nearest edge of the hole to the top, or bottom, … must be greater than or equal to 15% of the beam depth.”
Fifteen percent of 15 in. is 2.25 in. Our hole is 5 in. – 2 in./2 = 4 in. from the bottom; good.
“8. Where multiple holes are present, the nearest edges of adjacent holes must be separated by a distance equal to or greater than the largest of (1) 12 in., (2) the beam depth, and (3) four times the hole diameter …”
In our example the holes are about 4 ft apart; good!
Now let’s do some calculations.
The beam in question is a floor beam carrying an Occupancy Live load, Dead load, and its self weight totally 535 pounds per linear feet (plf). To examine the permissibility of the 2 in. hole, the Shear and Moment at that location must be determined. From engineering mechanics (or, see, Figure 1 of the American Wood Council Design Aid No. 6),
V @ 2 ft = w (L/2 – x),
where
w = the applied load, 535 plf,
L = the span, 20 ft,
and x = 2 ft. Thus,
V @ 2 ft = 535 plf (20/2 – 2 ft) = 4280 lb.
M @ 2 ft = (w x / 2 ) (L – x) = ( 535 plf x 2 ft / 2) (20 – 2) ft = 9630 lb-ft.
Now let’s see what the Shear and Moment capacities are at the hole, to see if the hole is permissible.
First the new centroid of the section must be calculated.
Using Equation (1) on Page 3,
y (centroid, measured from the top) = (d2 – 2 du v – v2)/[2 (d – v)],
where
d is the beam depth, 15 in. in our case;
v is the dimension of the hole perpendicular to the beam axis, 2 in.; and
du is the distance from the top of the beam to the top of the hole, 10 – ½ of 2 in. = 9 in., for our beam.
Thus,
y (centroid) = (152 – 2 (9) (2) – 22) / [2 (15 – 2)] = 7.115 in.
Equation (2) on Page 4 of the Tech Note is then used to calculate the Moment of Inertia of the section at the hole:
Inet = b [ d3/12 + d ( d/2 – y centroid)2 – v3/12 – v (du + v/2 – y centroid )2 ].
For our beam this gives … 1364 in.4.
The Section Modulli at the hole are:
S1 = I / y centroid = 1364 / 7.115 = 192 in.3 with respect to the top of the beam, and
S2 = I / (d – y centroid ) = 1364 / (15 – 7.115) = 173 in.3 with respect to the bottom.
The governing Section Modulus, Snet, is the lesser of the above, in our case, 173 in.3.
The Design values for the beam are Fb = 2400 psi and Fv = 265 psi (Douglas fir – Larch 24F-V4).
Thus the (Allowable) moment capacity at the section is,
Fb CD CM Ct (CV or CL) Snet.
The Design values for the beam are Fb = 2400 psi and Fv = 265 psi (Douglas fir – Larch 24F-V4).
In our case C D is 1.00, C M and C t are assumed to be 1.00. The Volume factor for bending is calculated to be 0.98, and the Beam Stability Factor, C L is assumed to be 1.00 (top of beam braced laterally).
Thus,
F b C D C M C t (C V or C L ) S net = 2400 psi (1.0)(1.0)(1.0)(0.98) 173 in. 3 = 406,900 lb-in. = 33,900 lb-ft .
Since the design moment at the section is 9630 lb-ft, the section with the hole is `good’ with respect to bending moment (9630 ≤ 33,900).
Per Technical Note 19 the Shear force and Shear stress concentrations must also be investigated at the section of hole. The Shear force is investigated using Equation (5):
(is) … V @ hole ≤ 2 b (d – v) Fv CD CM Ct Cvr / 3 (?)
For our example,
(is) … V @ hole = 4280 lb (from above) … ≤ … 2 (5.125) (15 – 2)(265 psi) (0.72) / 3 = 8475 lb? … Yes; good!,
where
again, CM and Ct are taken to be unity (not wet, not hot),
and
Cvr = 0.72 (applied to non-prismatic sections, beams with notches, etc.).
Shear stress concentrations are evaluated using Equation (6):
(is) … (3V/2bd)(1.23 + 0.82 h/d) + (0.6 M / bd2 x h/d) ≤ 1.6 Fv Cvr CD CM Ct Cvol (?),
where
Cvol = (1 in.3/v2b)1/5.
For our example,
Cvol = [1 in.3/(2 in.2 5.125 in.)]1/5 = 0.55.
Equation (6) then goes on to be
(is) … 3 (4280 lb)/2 x 5.125 in. x 15 in.)(1.23 + 0.82 x 2 in. / 15 in.) + (0.6 (34,600 x 12 lb-in.) /(5.125 in. x 15 in.2 x 2 in./15 in.) ≤? 1.6 (265 psi) (0.72)(1.0)(1.0)(1.0)(0.55) , or …
(is) … 120 psi ≤ 167 psi? Yes. Good.
The 2 in. hole 2 ft from the end satisfies all three calculation checks (Equations 4, 5, and 6 in the AITC Tech Note), as well as the overall limitations. The hole that was `not good’ without engineering analysis … is good, with.
References
Evaluation of Side Holes in a Glulam Beam, Jeff Filler, Yahoo! Contributor Network.
Beam Design Formulas with Shear and Moment Diagrams, Design Aid No. 6, American Wood Council, Washington, D.C.
Use of the Volume Factor in the Design of Glued Laminated Timber Beams , Jeff Filler, Yahoo! Contributor Network.
Guidelines for Evaluation of Holes and Notches in Structural Glued Laminated Timber, Technical Note 19, American Institute of Timber Construction, Centennial, CO, July 2012.