How to Make Native American Style Open-Fired Pottery with No Special Tools or Kilns
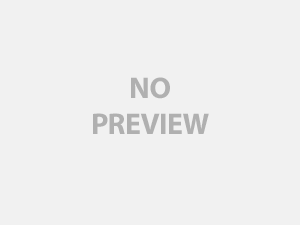
Low-fire clay is clay that will fire at temperatures that can be reached in a ground fire. While modern pottery techniques rely on much higher firing temperatures, the use of low fired clay allows you to fire your clay in your backyard!
Commercial clays fire at specific temperatures because they have been specially formulated to do so. A variety of materials are mixed with commercial clay to give it specific properties. Low fired clay, however, can be used essentially the way it comes out of the ground. Clay that is flexible enough to be rolled into your hands to form a snake then wound around your finger will likely be suitable for using for open-fired pottery.
Fortunately, clay that is suitable for ground firing can easily found in the wild. That’s the way the Native Americans did it after all. There were no Hobby Lobby’s or Michael’s to run to when you needed clay. Natural clay was harvested from alongside streams and other water bodies.
Contemporary potters typically place a lot of importance on tempering clay before it is used. Personally, I don’t think this step is always necessary. These potters go to all lengths to take out all vegetation, sand, etc. and then add what is essentially the same stuff back in the form of temper! I have personally used clay straight out of the ground to construct perfectly functional pottery.
While my beliefs run counter to what the experts contend pre-contact Native Americans did to prepare their clay, I continue to contend that they probably did little more than what they absolutely had to do to get a working pot or other clay item! Native Americans would likely have picked out bigger sticks, pebbles, etc. but I doubt seriously they went to great lengths to thoroughly clean their clay. It has been my experience, in fact, that all you have to do to get sufficiently clean clay is dig down a couple of feet into your supply! While the top layer of a clay deposit may have a lot of vegetation in it, just a few inches under the surface will be really nice stuff.
I think clay preparation in pre-contact time was largely determined by needs of a particular situation. According to the distance of the clay supply to the homes of the potters, for example, clay might have been dried to lighten it up for transport. It would then have to be remoistened before use. If clay supplies at home were running low it would have been desirable to extend those supplies by adding sand or dirt or vegetative material. Today we call that type of addition temper and insist that it is needed to make a functional pot. Again, my experience would indicate this is not always the case.
If you do dig your clay, the most important thing you should watch out for is making sure you are getting clay that is free from chemical contamination from pollution. If you can’t find a suitable natural deposit of clay then you can easily order low fire clay from any pottery supply shop. Whatever your source, the steps involved in making a pot and firing it in an open ground fire are essentially the same.
You want your clay to be moist but not dripping in excess water. Figuring out the best moisture level is a process of trial and error. If the clay is muddy enough to leave more than just a little residue on your hands then it is too wet. If the clay is forming small surface cracks as you work it then it is too dry.
The items you can make from clay are practically limitless. Keep in mind that it is important to work all of the air bubbles out of the clay both before you start forming your project and during that formation. Trapped air bubbles will cause the piece to crack when you try to fire the piece.
To make a small pot you can either use the coil method or the pinch pot method. To me the pinch pot approach is a lot more intuitive. Simply take a lump of clay about as big as your fist. Knead it to a smooth consistency and role it into a ball. Next poke your thumb into the center of the ball and start slowly working the hole that is formed out bigger and bigger by pinching your thumb towards the rest of your fingers.
As you work on expanding your initial hole, slowly turn the ball of clay around and around so that you pinch evenly around its whole perimeter. Slowly the walls of your pot will begin to emerge. Keep working evenly around the pot making the walls thinner and thinner.
Make sure you work the bottom of the pot as well by poking your thumb downward evenly around the surface of the pot’s inside bottom. Turn it over and pay some attention to the outside of the pot as well. Smooth it with your fingers and work to make the wall thickness consistent all around the pot and on its bottom. As long as no holes emerge, you can’t make the walls too thin. You can, however, make them too thick. Ideally you want a wall thickness around 1/8 of an inch.
As you work the surface of your pot may begin to get dry and form small cracks. Dribble on a little water and spread it evenly across the pot. Work the surface until the small cracks disappear. Then begin to pay more and more attention to smoothing both the outside and the inside of the pot.
Once you are satisfied with your pot’s wall thickness, smoothness, and symmetry you can set it aside to dry some. When the clay has reached what is called a leather dry stage you can use a smooth stone to burnish its surface to a shine. Next you can incise a design into its surface using an awl or even a pin. Just make sure you don’t puncture the wall while you are doing so.
The next step in your pottery experiment is very critical. The pot must be chalk dry before you can even start to think about firing it. The time it will take to achieve this will vary with your climate. Dry it slow at first. Don’t put it into direct sunlight and keep it where air can circulate around it freely. Turn it upside down on its rim for part of this time so that the bottom can fully dry.
When you think your pot is completely dry, dry it more! You can even put it on the dash of a hot vehicle at this point. The sun will help you make sure that the pot is indeed completely dry before you start to fire it.
While firing a number of articles at once can be tedious, firing just one pot is pretty easy. Build a very small campfire and set the pot just inside the heat from that fire but not inside its flames. It doesn’t matter what kind of wood you use as long as it is good and dry and you keep the fire burning. Turn the pot every few minutes so that another part of it is facing the fire. Over time slowly move it closer and closer to the fire.
Eventually, your pot will be almost too hot to touch and be just outside the fire itself. At this point it is easier to move the fire than the pot! Carefully rake some coals towards the pot, to either side, and to its back. The idea isn’t to keep the coals burning but just to heat the pot up evenly to an even higher temperature than it was up until this point.
Carefully position more and more coals around the pot listening carefully to hear if there are any subtle popping sounds that indicate the pot is cracking. Slowly start adding very small diameter sticks to the coals so that the flames begin to flare up.
The idea in open firing is to move in slow motion. Don’t try to rush the firing process or you’ll end up with pot shards rather than a usable vessel. The whole firing process will take you a couple of hours and most of that time has been spent between the time you first placed the pot near the fire and now.
Slowly add progressively larger pieces of wood until you have a good sized fire burning all around the pot. Once that is the case you will then need to build the fire up so that the flames are several feet high. Add small dry sticks and carefully watch the pot in the coals. When the pot is glowing orange the firing process is complete! Keep adding small dry sticks until you achieve that orange glow.
The final step in firing your pot is slowly cooling it down. Allow the fire to die completely down on its own. Just don’t add any more wood. Don’t plan on removing the pot from the coals until the pot and the coals alike are completely cool to the touch.
Making and firing pottery the way the Native Americans did it liberates you from the equipment considerations that make so many hobbies impractical from a money perspective. This pottery, or any other fired items you elect to make and fire, can be ever bit as beautiful and as functional as a pot produced in a multi-hundred dollar kiln.