How to Make a Quick but Sturdy Cabinet Door
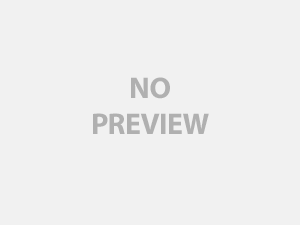
When I had to make a batch of pantry cabinets in a hurry and at a low cost, I developed the design for this frame-and-panel door. I wanted the door to have a traditional flavor and reasonable strength but obtained with the least possible labor and materials. I decided to use a plywood panel and dress it up with a simple quirk-and-bead molding. I planned the simplest joinery I could, and then I decided to apply the molding instead of milling it onto the frame pieces. The molding is easily made with a stock router bit, and the quirk, or recess, behind the bead produces a dramatic shadow that gives the flat-paneled door its visual weight. The design is well-suited for small- or medium-sized doors on kitchen cabinets, vanities, and built-in storage units and will look as good painted as with a clear finish.
Grooving Non-Stop
I chose ¼-inch plywood (good on both sides) for the panel to keep the door light and stock preparation to a minimum. Frame-and-panel construction accommodates the expansion and contraction of a solid panel by allowing it to float in the frame. Here, with no wood movement to worry about, I was able to glue the panel on all four sides, making it a structural element of the door. I greatly simplified the joinery by housing both the panel and the rail tenons in the same ¾-inch-deep groove. At ¾ inch, the tenons are somewhat short, but the plywood panel glued all the way around at full depth in the groove adds considerably to the door’s strength.
This technique not only removes the need for making separate mortises for the tenons but also means that you don’t have to stop the grooves on the stiles as you normally would with frame-and-panel doors. Instead, you just run the grooves the full length of all the frame members.
I usually plane my frame stock ¾ inch thick and rip the pieces 2 inches wide. Then I groove the inside edge of each piece on the table saw. Because ¼-inch plywood is usually somewhat less than ¼ inch thick, I don’t bother with dado blades. I just cut the groove in two passes with a regular blade raised to ¾ inch. However you cut the groove, it will be helpful to mill extra stock with the frame members for use as test pieces as you seek the setting that will give the panel a snug fit.
Rails Get Tenons
Next, I cut the cheeks of the tenons. Because the tenon length is the same as the groove depth, I leave the table saw’s blade at the same height I used to cut the groove. I mount the rails onto a simple, shopmade jig for safety and support.
I cut the tenon shoulders on the table saw using the miter gauge. I use the fence as an end stop, which is permissible here (though it isn’t in normal crosscutting). That’s because I’m not cutting all the way through the piece, so there’s no danger of kickback or jamming. You could also use a stop block clamped to an extended fence on your miter gauge.
Size Up the Panel
I use ¼-inch cabinet-grade plywood for the panels in most doors like these. For larger or heavier-duty doors, it would be advisable to split the panel with a medial rail or use ½-inch plywood and rabbet around the back to produce a ¼-inch tongue.
When I cut out the panels, I take particular care to ensure that they come out square. Then, when I glue up the frame members around them. I can rely on the panel to make the door square and the glue-up trouble-free.
Attending to Assembly
When I assemble the doors, I apply glue generously in the grooves and on the tenons. Then I lightly clamp the rails and stiles around the panels. Next, I double-check for squareness and clean up the glue squeeze-out. After removing the clamps, I clean up the frame and fair the joints with a sharp block plane.
Quirky Molding
The quirk-and-bead molding can be produced from excess frame stock with a beading cutter in a router. I bead all four corners of the stock on a router table or simply a router upside down with a fence clamped to the base. To free the pieces of molding, I cut a kerf down the middle of each edge and then rip through the full thickness of the stock.
I cut the miters for the molding on the table saw with the miter gauge, but the miters can be cut nearly as fast with a dovetail saw and a block plane for fitting. First, I dry-assemble the molding. Then I glue it in with yellow glue and hold it in place with masking tape. I close minor misalignments at the miters by pulling the molding away from the frame slightly. The tiny gap created behind the molding won’t be noticed – it will read as part of the shadow that gives this simple molding its distinction.