How to Work with Translucent Polymer Clay
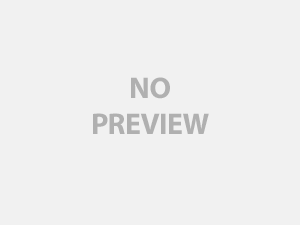
First, a definition
This clay is translucent, which means some light can shine through it, allowing whatever is in, behind, or under it to show through. However – that doesn’t mean it’s perfectly clear. If it were, it would be described as transparent instead.
In its raw form translucent clay looks milky white. How clear it gets after curing depends on many factors, including thickness, baking temperature and time, and whether it’s used alone or with inclusions added.
Suggestions for improving the clarity of finished pieces
Translucent clay is used mainly for its ability to “reveal” other colors and objects. Most of the time people want it to be as clear as possible. Here are a few things you can do to enhance this clarity:
– Condition and handle the clay as little as possible. One artist suggested only one “run” through the pasta machine to even out the thickness. That would never be enough to condition other kinds of clay, but for translucent it seems to work – for her.
– Use as thin a piece as possible.
– Try curing at a different temperature – slightly higher (maybe 290Ã?° or 300Ã?°F) or lower (maybe 250Ã?°F) – or for a shorter or longer period of time. I’ve had the best luck with 250Ã?°F for 20 minutes, repeated after the pieces cool (if they’re thicker than a quarter inch) to make sure they’re adequately cured. If you do try the higher temperature or longer time be careful not to burn the clay; turn the heat down immediately or remove the piece from the oven if you smell burning or other fumes.
– Immediately after curing, remove the piece from the oven and put it in ice water.
– Cover the piece while curing, either by putting it in a covered container, placing it face down on the baking sheet, or spreading cornstarch liberally over it.
– After the piece has cured – and cooled – sand it vigorously under water. (To avoid breathing in clay dust, you should always sand polymer clay this way rather than in the open air.)
Feel free to try any or all of these suggestions. But remember that translucent clay will never be as clear as glass.
Potential problems and how to avoid them
Translucent clay has a tendency to develop “plaques” – small opaque areas that are usually shaped like a half moon. Unfortunately, these areas aren’t usually visible until after curing, and can really affect the look of the finished piece.
Some artists just find a way to incorporate the plaques into the design of the object, especially if they’re trying to imitate a semi-precious stone. If you’d like to minimize plaques the best way seems to be to handle the clay as little as possible before curing. This is also a good way to cut back on bubbles – something that translucent clay seems more prone to than the colored clays (possibly because of the absence of pigment to “firm up” the clay slightly).
Translucents also may turn brown or yellow more easily in the oven. The best suggestion for this problem seems to be to cover the piece while it’s curing – similar to what you’d do with the edges of a pie crust when you cover them with aluminum foil. In the case of clay, the best cover seems to be cornstarch, which can be washed off easily after the piece has cooled.
Translucent polymer clay can be used to create many different special effects. But those effects can be ruined by some of its potential problems. Give this clay a little extra TLC, while you’re working with it and when it’s curing. The final result will be worth the effort.