Interior Residential Foundation Details
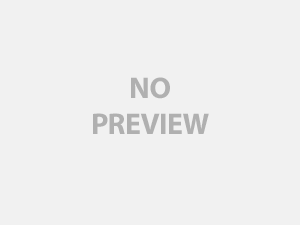
- Introduction
- Foundations for Bearing Walls (Gravity Loads)
(Diagonal Tension)
- Details
- Foundations for (Interior) Braced Wall Lines
- Conclusion
- References
1. Introduction
Now we address the interior foundation / footing situation. As discussed in an earlier lesson, we will need a foundation / footing where required for: 1) support of gravity loads from above, and 2) bracing (braced wall lines and/or shear walls). Gravity loads (weights of structure, occupants, etc.) will come down through our structure to the foundation via bearing walls or as point (concentrated) loads via columns. We will deal with loads from bearing walls here; foundations for column (point) loads will be dealt with later. We will also deal here with continuous foundations required by braced wall lines. Efficient planning in the design development stage of a project will result in interior foundation elements serving to support gravity loads and braced wall lines. Stated differently, good planning of the superstructure above will result in utilization of walls and wall lines for as many common purposes as possible. Poor planning will result potentially in additional foundation elements, or maybe even `engineering’, if the design cannot be `crow-barred’ into the prescriptive requirements.
2. (Interior) Foundations for Bearing Walls (Gravity Loads)
Some common foundation types for interior bearing walls are listed below.
- Thickened slab footing
- Concrete slab on grade over slab/strip footing
- Strip footing in Crawl Space
- Beam(s) with posts
The thickened slab footing is common and is convenient in that it can be cast (poured) at the same time as (continuous with) the floor slab. (The `footing’ part is simply a deeper dug `trench’ into which concrete is cast along with the slab.) If it is poured one-piece with the surrounding slab, then the dimensions of the footing are generally taken to be the footing width x the entire thickness. If the slab is poured separately from the strip footing (e.g., at a later time), then the structural dimensions of the footing should not include the slab.
Structural dimensions and details of the footing are obtained prescriptively, or, by calculation. Using, for example, Tables R401.4.1 and R403.1 of the International Residential Code, the designer determines a presumptive allowable soil bearing pressure based on soil type using Table R401.4.1, and then the minimum footing width using Table 403.1 based on type of construction and number of floors supported. Section R403.1.1 then goes on to require that the footing thickness be greater than the projection of the footing past the face of the (in this case interior) wall, and not less than 6 in., essentiallyin the same way we dealt with exterior foundations. Things are a little different here in that the interior wall is often not concrete, either being a wall framed onto the concrete slab, or a short framed wall across the crawl space.
(Diagonal Tension)
The `minimum thickness thing’ basically recognizes that concrete generally shears at 45 degree angles (so called `diagonal tension’). If one sketches a potential diagonal tension crack starting from the face of the wall and then going across the footing, the soil bearing (up) on the footing `within’ this crack tends to compress the concrete (and remember concrete is strong in compression, really strong), and (only) the soil bearing upward `outside’ this crack tends to effectively shear the footing. So, if we make the footing always deeper than the `projection’ of the footing past the wall, this 45 degree `potential crack’ line doesn’t even come out on the bottom of the footing; it comes out on the side. So, no soil pressure is effective at shearing (cracking) the footing – the footing won’t shear.
And, generally, for the modest loads that accompany prescriptive Residential construction, if it wide enough to not fail the soil (essentially satisfying Tables R401.4.1 and R403.1), and it is thick enough to not shear, it will also (generally) be strong enough to not break (in bending), and thus we generally do not have transverse reinforcement (going across the footing). We will have, however, longitudinal reinforcement (going the length of the footing), prescriptively provided.
If we want (or need) to calculate the footing dimensions, we essentially cover the above process by calculation:
- determine the footing width based on the allowable soil pressure (so we don’t `fail’ the soil)
- determine the minimum footing thickness so we don’t fail the footing, in shear
- determine transverse reinforcement needed (if any) so the footing doesn’t break in bending (by the soil pressure acting upward and breaking off the `projecting’ portion).
The first item above we covered in an earlier lesson … here.
By making the footing deeper (thicker) than the projection past the face(s) of the wall we know it won’t shear because we don’t develop any effective shearing stresses. If we don’t want to make the footing that thick, then we need to calculate the effective shear stresses and make sure they aren’t enough to crack the footing. But once we start trying to make our footings as `thin’ as we can, we will find that we will also be making them vulnerable to breaking, in flexure, and will need transverse reinforcement. All these calculations will be shown later, but for now, just make the footing thicker than the projection dimension(s), and be done!
3. Details
Many of the detail items for an exterior foundation (earlier lesson here) carry over directly, or kind of directly, to an interior foundation. I list them below (as listed in the earlier lesson) with or without much comment.
- Stem wall height … yes, if we have a pony wall we need to detail the pony wall height or elevation. If our floor situation is a slab then the slab elevation needs to be detailed.
- Stem wall thickness … if a pony wall then the nominal wall framing dimension should be specified.
- Footing thickness … includes or excludes slab on grade thickness depending on whether poured monolithically or separately. In either case generally not less than 6 in. Typical slab thickness values range from 4 in. to 6 in., with Residential applications generally 4 in. Local codes may allow 3-1/2 in. minimum (4 in. nominal).
- Footing width … yes.
- Stem wall reinforcement … not applicable, unless the crawl space wall is concrete, but this is uncommon (at least around here).
- Stem wall vertical reinforcement … ditto with above.
- Key … not applicable in the case of a framed wall; not common if concrete wall.
- Longitudinal reinforcement … yes, definitely, either prescriptive or calculated. NOTE: slab reinforcement is additional to the Longitudinal Reinforcement. Slab reinforcement might be welded wire fabric or # 3 or # 4 bars on 12 in. or 18 in. o.c. each way. Ratio of reinforcement area to slab area should not be less than 0.0018 for Gr. 60 reinforcement.
- Transverse reinforcement … not common.
- Supporting soil … important! … needs to be undisturbed native material or fill certified to meet the specified allowable soil pressure. (Now, having said that, I recognize that a lot of interior residential footings are placed on gravel fill that has not been certified (by a Soils Engineer). Probably a lot of building officials just nod `yes’ if it looks reasonably compacted. Here is where I remind you (the reader, the student, the whoever) … build on fill at your own peril. Maybe it will be okay, fine, no problem. But foundations are hard to fix; quality control is the responsibility of the Owner; and by the time there is a problem the Contractor’s phone number will no longer be working; and the building official will simply remind you of `quality control is the responsibility of the Owner’ part of the code.
- Drain … generally not needed as it is assumed that the perimeter is sufficiently drained. However, water has a way of moving in strange directions, including up. Some familiarity with local conditions is helpful here.
- Backfill … not really applicable.
- Waterproof coating … ditto.
- Finish Grade … make sure that the footing and finish grade are `deep’ enough to accommodate crawl space requirements if a crawl-space type foundation is used.
- Anchor bolts … generally it is the preference of contractors to NOT use cast-in-place anchors for interior strip and slab footings as they `get in the way’. Where anchor bolts are required, say, for a braced wall line, or braced wall panel, generally the `equivalent‘ in a post-pour anchor is allowed … the so-called `expansion bolt’ for example. For interior walls that do not carry significant lateral loads lighter anchoring devices may be allowed (powder-actuated fasteners, for example).
- Sill seal … not applicable.
- Sill plate … yes, if there is a framed wall. Check with local requirements and experience as to whether this must be preservative treated. Where I practice there is a lot of moisture everywhere for about half the year so ANY wood in contact with concrete (in my details) will be detailed as needing to be preservative treated.
- Crawl space … yes, if applicable.
- Interior grade … already discussed under Finish grade. NOTE: local requirements might include pea-gravel and vapor barrier over exposed soil in crawl space. Check with local requirements.
- Energy code requirements … again, not shown … (I’m a structural person).
- OG vs. FG … just make sure you don’t build on fill :).
- Stepped (interior) footings … rare … generally grade changes are accommodated at intersecting (other) walls (unless the interior wall is concrete).
- Foundation drain (outlet) … not applic.
- Roof drain … not applic.
- Other.
4. Foundations for (Interior) Braced Wall Lines
Foundations for interior braced wall lines must accommodate the lateral load coming down through the plane of the wall. In many cases the braced wall line foundation will also accommodate gravity loads coming down through the wall, but not always. Referring to the attached sketch, I note some important details of an interior foundation (this one with framed crawl space wall) that receives lateral loads from a braced wall line.
- Footing dimensions – either prescriptive, or determined from gravity loads. Footing must be placed on undisturbed native material or engineered (certified) fill. (See note below on thickness.)
- Longitudinal reinforcement – prescribed or calculated, but not less than 2 – # 4 (in my opinion).
- Preservative treated plate – unless not required and demonstrated to not be needed.
- Anchor bolts – size and spacing prescribed; generally a post-pour (and shallower) equivalent is preferred.
- 2 x 4 or 2 x ____ @ ____ in. o.c. framing …
- Sheathing – the pony wall must be sheathed and nailed (on at least one side) per the braced wall line and other prescriptive requirements.
- Where joists are perpendicular to the pony wall blocking must be provided to carry the lateral load across the floor space.
- Floor sheathing nailing requirements (to joist or blocking) at the braced wall line must satisfying the braced wall line fastening requirements and the requirements of the floor manufacturer.
- The sole plate of the wall above must be nailed through the floor to the joist or blocking per the braced wall fastening requirements (e.g. 3 – 16d per 16 in.).
- Fastening Schedule – the elements described above must be fastened properly so as to be able to provide a path for the lateral load in the structure to be carried out to the foundation. See Table R603.1 in the International Residential Code or Table 2304.9.1 in the International Building Code.
If you want to see something really cool, get (download) the ES Legacy Report for the fasteners( … here). It gives `equivalents’ for the above fasteners … say if the Contractor wants to use a different nail, for example, and not only that … it gives illustrations of the various fastener conditions in the IRC and IBC tables.)
Note (on thickness): footing thickness may be dictated by anchors. If deep anchors are required, the footing thickness must be at least the depth of embedment of the anchor plus the 3 in. concrete cover distance if the footing is cast against earth.
5. Conclusion
Again it seems we have arrived to a point where we have covered an exhausting amount of stuff, whether or not we are `done’. But at least we’re done for now, and other stuff will be covered in other lessons.
6. References
International Residential Code, International Code Council, 4051 West Flossmoor Road, Country Club Hills, IL 60478.
International Building Code, International Code Council, 4051 West Flossmoor Road, Country Club Hills, IL 60478.
ES Legacy Report, NER-272, International Staple, Nail, and Tool Association, 512 West Burlington Ave., Suite 203, La Grange, IL 60525.