MIG Welding 101: Replacing the Welding Tip
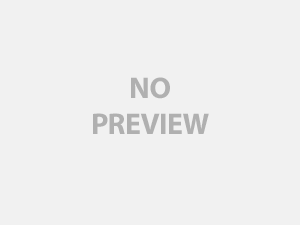
First, pull off the outer nozzle. Simply grab the brass nozzle portion of the MIG gun tip and pull. It should come off easily and without hassle; if it doesn’t, try giving it a little twist while you pull. Once removed, clean the inside of the nozzle with a round wire brush or MIG pliers to ensure a debris-free surface before you put it all back together and strike an arc.
To clean the nozzle with MIG pliers, just stick the nozzle onto the tip of the needle-nose portion and twist vigorously until debris stops falling out of it. Then hit it with a rag if there is one handy. The same thing goes for the wire brush method – just insert it and start scraping the edges.
Next, unscrew the welding tip itself. You SHOULD be able to loosen this item with just your fingers. However, if it does not want to budge, lightly use a pair of pliers on it, being careful not to mar any surfaces or bend things up. The tip will probably be black and crusty, which is fine because it is going in the trash, anyhow. I have heard of folks cleaning them up and whatnot, but it isn’t worth it – these things are pretty cheap.
What I do after the MIG tip is off is completely clean the area with a standard wire brush and a rag. The goal is to get everything shiny and free of dirt and debris so your next weld will be a quality one. I’m sure we have all heard the old adage “take care of your equipment, and it’ll take care of you.” Once you have inspected and come to the conclusion it all looks good, it is time to start reassembling the MIG tip.
If you are using .030 wire, get a .030 tip, and the same goes for .035 and every other size. The correct tip will help the current pass through to the weld, creating a much cleaner, trouble-free weld. Screw the new tip in where the old one came out, and make it snug, but NOT over tight. As a general rule I tighten mine in by hand as tight as I can get it, then give it the smallest of bumps with pliers. The MIG tip helps current and wire flow, so you want this part right. After you are convinced the MIG tip is back in the gun and ready to fly, replace the outer nozzle and give her a go! If the tip was in real bad shape, you will notice an immediate change both in the weld quality and the wire flow. It is recommended for the casual welder to replace the tip after every 100 pounds or so of wire has gone through it, but if yours goes bad more often, replace it sooner! It is also recommended to junk any MIG tip that has been dipped into the molten weld pool.