Material Takeoff Tips in Finish Carpentry
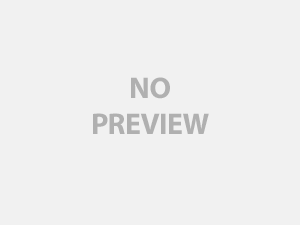
Before you can order materials, you must be able to determine how much of each one is required. This is done by drawing up lists called takeoffs.
Since the cost of finish materials is relatively high, it is wise to calculate the amounts you will need as accurately as possible. It also helps to visualize the completed details of each job, which makes for more efficient ordering and less waste.
Materials takeoffs can be generated by taking off the required amounts from the architectural drawings, or by measuring at the job site, or both. If the drawings truly reflect the actual construction, you can determine the various lengths of materials quickly by using an architect’s scale, a ruler that allows you to measure actual dimensions directly on the drawing. It is advisable to visit the job site with tape measure in hand, to verify the figures on the drawings and to take dimensions that are difficult to determine accurately from the drawings. Some lumber and millwork companies will do the takeoffs for you from your plans and provide you with a list and a quote on the price of materials.
In finish carpentry, materials are divided into two categories: those that are ordered and installed in random lengths, such as baseboard, chair rail, picture rail, and crown molding – and those that are ordered in specific lengths for a particular application, such as door and window casings, wainscoting frames, shelves, stair treads, and railings.
Materials in random, or running, lengths are ordered and delivered to the job site in whatever lengths are available. For example, baseboard stock, ordered in random lengths, may arrive at the site in sections varying from 4 to 16 feet. The total count, say 450 linear feet, would come from the sum of all the individual room measurements using that type of baseboard, plus about 10 percent to allow for waste and errors in cutting.
Materials ordered in specific, or standing, lengths are installed at the particular locations for which they are ordered. In this instance, you would order exterior door casings as follows. For a standard door height of 6 feet 8 inches, the side casing material is 7 feet long and the head casing approximately 3 feet long. The sum of these lengths is 17 feet. Noting that the material is sold in multiples of 2 feet, you would have about 1 foot of waste material.
This method works primarily for exterior door (and window) casings. The drawback for ordering interior door casings is that 18-foot lengths of interior casing are often special-order items, so the savings in waste may be more than offset by the premium price of the material. A better method, with less waste, for interior door and window casings is as follows. For doors, order three 14-foot lengths of casing and you will get four 7-foot side casings and two 3-foot head casings, enough for both sides of one door, with one 7-foot side casing left over for the next door. This reduces the waste to less than 1 foot per door. If the casings aren’t available in 14-foot lengths, two 10-foot lengths and two 8-foot lengths will do, although this will yield two 1-foot sections of waste material per door.
When ordering other finish carpentry materials, such as shelves and closet poles, stair treads, risers, and railings, a method similar to standing length is used to calculate the amounts. The length of each item is determined and then multiplied by the number of those items.
When ordering wallboard and paneling, you must calculate areas to determine the amounts. Calculations for wallboard are done as follows. Measure the widths, lengths, and heights of the wall and ceiling surfaces. Multiply these to obtain the area of each surface. Sum up the surface areas to find the total area. Divide this total by the area of one sheet to determine the total number of sheets required.