Selecting the Right Lumber Makes Woodworking a Joy
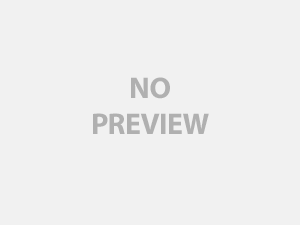
For me, one of the more exciting times in a woodworking project is the afternoon I spend picking out just the right boards from the local hardwood yard. Pulling one plank at a time off of the top of each bin and examining it for grain, color, sapwood, wane, cupping, etc. takes time. Putting the rejects aside and setting the keepers in their own pile, I slowly work through the stacks of my chosen material. It can, and usually does, take hours to find the handful of planks that will evolve into whatever it is I plan on building.
Like all aspects of woodworking, this process is not to be done when rushed. Making a mistake here can cause the entire project to be more difficult than it needs to be, and can dramatically impact the finished piece. I learned this the way I learn most things, by making the mistake myself and suffering with the consequences.
I was working on one of my very early woodworking projects. My wife and I had just gotten married and she needed a set of bookshelves for the stained glass workshop she was setting up in our new house. Nothing fancy – just something utilitarian that fit the space. I was anxious to build our first piece of furniture and, after doing a quick design, I ran out and got the lumber that I hoped to transform into useful, if plain, shelves.
The lumberyard had some great looking red birch. It was deep in color and a few of the boards were highly figured. Without much thought, I grabbed the most striking pieces that were long and wide enough to fill the bill.
I knew something was wrong when they didn’t all lie flat in the bed of the truck. One of the boards seemed especially unruly with one end up in the air and the other pointed down into the truck bed. I didn’t pay much attention to it, though, thinking that it would be fine once I got it home.
A couple of days after getting the birch, I finally had time to get cracking on the bookshelves. It was a simple design with solid sides, top, bottom and immovable shelves. The back was to be made with lengths of birch shiplapped, with the edge of each board knocked off to form a slight v-groove.
I started by cutting and assembling the sides, top and bottom. Next I cut the three shelves and attached them to the sides with cleats and screws. By the time I got around to building the back of the unit, I only had one piece of birch left – the twisted board that didn’t lie flat in the truck. I had tried to use this board for the shelves and for the top and bottom, but I couldn’t get a single straight piece out of it that was long enough to be usable. It certainly wasn’t going to yield what I needed for the back, so I returned to the lumberyard for more birch. Unfortunately, they had none left that matched the tiger-striped stuff that I had bought earlier. I settled on a couple of plain planks, making sure they were straight before putting them in the ‘keepers’ pile.
I finished the bookshelf and, as I expected, the back didn’t match the rest of the unit. Once it was filled with books and stained glass pieces, it was hard to see the difference – for most people. That was years ago and I still get a little twinge of ‘I wish I’d done that better’ when I walk by it.
As for the offending piece of birch, I couldn’t bring myself to throw it out. I wanted to believe that one day it would be good for something, and I stuck to that conviction for years. I stacked some 8/4 oak on it thinking that would straighten it out, but two years later it was as twisted as ever. Eventually it moved with us to our second house where I tried to work it into project after project. But it simply wouldn’t yield a single piece of usable material. Finally, after measuring it, moving it, stacking it and cursing it for more years than I can remember, I took the circular saw to it and cut it into firewood. Even the six-inch pieces of scrap wouldn’t lie flat, but they burned well.