Shed Building 101
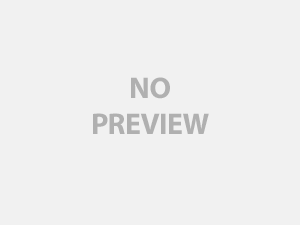
Ease of Assembly:
A good shed built at home will come with easy to understand instructions with clear step by step diagrams and well written explanations of what to do in each step. This however is not always enough, if the shed is manufactured well the pieces will all fit and screw in with EASE. There’s a big difference between a screw being able to fit and a screw being able to fit with ease. Designers may not always take into account what position the screwdriver and the individual holding the screwdriver or drill is in. Big sheds naturally take more time and require more man power i.e. 2 or more. By big, one means larger than around 70 square feet though it is always helpful to have an extra hand. Some of the tools and equipment needed for putting together a shed are a level, drill, gloves, tape measure, ladder, plywood and/or concrete, mason line, wood to keep concrete in place, and a shovel. Smaller sheds don’t always require concrete which makes them easier and more affordable to assemble.
Permit Requirements:
Depending on location a permit may be required to build a shed. In some areas any shed larger than 120 square feet requires a building permit from a local city hall after which building development may be inspected by a city inspector. Specific requirements in accordance with International Building Code must be adhered to if a permit is required. These things include fire safety, distance from property lines, anchoring to a concrete foundation and non-obstruction of water flow. While smaller sheds may not be subject to International Building Code they may be subject to municipal codes. It’s a good idea to call city hall before building.
In addition to the above two factors, it can be a good idea to consider things like necessity, building material, cost and implications to property value. For some, a shed is a necessity, especially if one has a big yard with a lot of upkeep requirements. Some people use garages for the tools but then again not everyone has a garage. Assessing one’s own storage requirements is important in deciding whether or not an Aluminum shed is worth the time, effort and cost. If the shed is built on site by the purchaser, the cost of the shed can decrease significantly. Many sheds come as kits and can be put together with a reasonable amount of effort and time. The cost varies based on the size of the shed, and type of material the shed is built from. While wood can be easier to work with, it is also more expensive, heavier and logistically more difficult than steel. However, steel that is not adequately maintained has the potential to rust quicker than aluminum which is also relatively lightweight.
Aside from the details, time and money required for building a shed, sheds are also quite useful. A shed can benefit a homeowner, Gardner /landscaper, carpenter, mechanic and others in many ways. Below are a few of those benefits.
-They help organize tools and yard clutter.
-Sheds can facilitate hobbies such as woodwork and mechanical work.
-Potentially increase property value.
-Help reduce clutter in the garage.
-Some sheds can also double as greenhouses, playhouses for children, and/or pool-side equipment and change room.
-Aluminum sheds may be stronger and more durable than other building materials if maintained and built correctly.
When considering a shed it is a good idea to take into account all the above factors. Sheds take a little planning and many people have the capacity to build them themselves. Shed kits can be freight delivered directly to a home via the Internet or by visiting a local garden and/or building center that provides such deliveries and merchandise. When building a shed consider the life of the shed, weather conditions and its usage requirements when assessing the size and location. Sheds that are easily accessible and in compliance with all relevant codes can be a pleasure, joy and contributor to the functionality of many homeowners and hobbyists.