Sheet Metal Workers – a Career Fabricating and Installing Sheet Metal
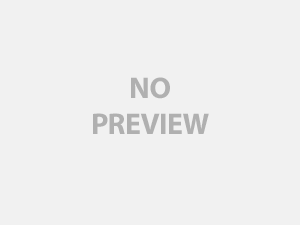
Many sheet metal workers are employed by building contracting firms that construct or renovate residential, commercial, and indus-trial buildings. Fabricating and installing air-conditioning, heating, and refrigeration equipment is often a big part of their job. Some workers specialize in adjusting and servicing equipment that has already been installed so that it can operate at peak efficiency. Roofing contractors, the federal government, and businesses that do their own alteration and construction work also employ sheet metal workers. Other sheet metal workers are employed in the shipbuilding, railroad, and aircraft industries or in shops that manufacture specialty products such as custom kitchen equipment or electrical generating and distributing machinery.
Fabricating is often done in a shop away from the site where the product is to be installed. In fabricating products, workers usually begin by studying blueprints or drawings. After determining the amounts and kinds of materials required for the job, they make measurements and lay out the pattern on the appropriate pieces of metal. They may use measuring tapes and rulers and figure dimensions with the aid of calculators. Then, following the pattern they have marked on the metal, they cut out the sections with hand or power shears or other machine tools.
They may shape the pieces with a hand or machine brake, which is a type of equipment used for bending and forming sheet metal, and punch or drill holes in the parts. As a last step before assembly, workers inspect the parts to verify that all of them are accurately shaped. Then they fasten the parts together by welding, soldering, bolting, riveting, cementing, or using special devices such as metal clips. After assembly, it may be necessary to smooth rough areas on the fabricated item with a file or grinding wheel.
Computers play an increasingly important role in several of these tasks. Computers help workers plan the layout efficiently, so that all the necessary sections can be cut from the metal stock while leaving the smallest possible amount of waste sheet metal. Computers also help guide saws, shears, and lasers that cut metal, as well as other machines that form the pieces into the desired shapes.
If the item has been fabricated in a shop, it is taken to the installation site. There, the sheet metal workers join together different sections of the final product. For example, they may connect sections of duct end to end. Some items, such as sections of duct, can be bought factory-made in standard sizes, and workers modify them at the installation site to meet the requirements of the situation.
Once finished, duct work may be suspended with metal hangers from ceilings or attached to walls. Sometimes sheet metal workers weld, bolt, screw, or nail items into place. To complete the installation, they may need to make additional sheet metal parts or alter the items they have fabricated.
Some tasks in working with sheet metal, such as making metal roofing, are routinely done at the job site. Workers measure and cut sections of roof paneling, which interlock with grooving at the edges. They nail or weld the paneling to the roof deck to hold it in place and put metal molding over joints and around the edges, windows, and doors to finish off the roof.