The Invention of Lithography and Offset Printing
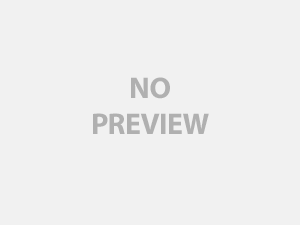
Alois Senefelder’s Brief Biography and the Life and Times of Alois Senefelder
Senefelder’s given name is Johann Nepomuk Franz Alois Senefelder. He was born in Prague in 1771. Senefelder was 24 when he discovered the process known today as lithography. Senefelder’s father was a noted German actor. Following in the footsteps of his entertainer father, Senefelder became a playwright.
He had the desire to sell his plays and hired a printer to print them. However, he was unsatisfied with the quality of the printing and resolved to print them himself.
Before discovering the concept of lithography, Alois was close to suicide when he found himself unable to provide for his mother and siblings. It was his discovery of a sprig of moss, which in turn gave him the idea for lithography, which saved his life. He started by using a needle and acid to etch his plays onto big, copper plates.
However, he soon discovered a different kind of process to doing this: using a flatstone, he would write on it with greasy chalk, then wetted the entire stone with water, applied the greasy ink to the entire stone, which in turn caused the ink to stick to the writing. Then, the stone would be pressed onto paper, which in turn would be used for printing purposes. This was the birth of lithography. Within twenty years of his invention, Senefelder’s lithography idea had spread to England and the United States.
The Invention of Lithography and Stone Lithography in America
Lithography is Greek for the words Senefelder used to describe his new method: stone printing. It took a full four years for Senefelder to perfect his process.
Before his discovery, there were only two kinds of methods for printing: relief printing, in which you create an image that protrudes from a plate and when you ink the surface, ink hits only the parts that stick out. The second method is intaglio printing, in which you can cut an image into a plate, ink the whole thing, and then wipe the surface clean. Ink stays in the depressions and transfers an image to the paper.
Senefelder died in 1834. By the time he died, lithography had taken off and became the primary way of printing.
Alois Senefelder’s treatise on lithography was first published in 1818. It discussed printing in colors as well as printing in black. His book served as a guide for printers worldwide throughout the early years of learning lithography.
The Invention of Photography and It’s Importance in Offset Presswork
During the early 1800’s, the advancements being made in the field of lithography were being made in small, paced measures. The process of making lithographic plates proved to be a long, laborious process. At this point, the search was on for an easier and quicker process for making process. This is when photolithography was born. And from there, the process of offset printing came about, which changed the face of lithography and the printing world as a whole to become more like the way we know it presently.
Photolithography was the marriage of photography and lithography. Photolithography is defined as the act of making a lithographic printing plate using photographic means. Photolithography was invented by Alphonse Poitevin, who was a French chemist, in 1855. The process went as such: He coated the stone (grained for halftone picture) with a solution made up off potassium bichromate and albumin and equalized the coating with a towel. He then dried it, exposed under a negative, washed it with water, and rolled up with greasy ink, which only adhered to the parts, which had become insoluble by exposure to light, but did not adhere to the moist parts. The stone was then etched and printed in the usual lithographic way.
The invention of photolithography was extremely important to the process of lithography itself. However, even with new processes in halftone photography, photolithography and process color printing, lithography needed a medium in which the limitations of the lithographic press were not as extreme. This is when offset printing became that medium.
The lithographic offset press had its debut in England in 1875. The press consisted of a lithographic stone flat bed press designed for metal decorating (printing on metal). An intermediate cylinder, covered with a specially treated cardboard, transferred the printed image from the litho stone to the sheet metal.
Ira Rubel and the Invention of the Offset Press
The lithographic offset press is what brought lithography to relative importance within the printing industry. Ira Rubel, who was a paper manufacturer from New Jersey, gets the credit for the first credible use of the offset press. He produced sulphite bond, then lithographically converted it into bank deposit slips.
Most will agree that Rubel discovered the use of the offset press for paper printing in about 1904 or 1905.
Now, Rubel’s press was quite fascinating actually. It was described as such: a flat bed stone machine. This machine was equipped with a rubber covered impression cylinder to help in the transference of images from stone to paper. When the feeder, which was a person, missed feeding a sheet while the press was running, the stone printed its image to the rubber covered impression cylinder. The next impression then had an image on both sides: direct litho on the front as well as an image transferred from the rubber onto the back. Rubel noticed that the image on the back was much sharper than the image on the front.
It was at that point that Rubel decided to design a press in which the image was printed from the plate to the blanket and then to the paper. Between himself and another lithographer, A.B. Sherwood, they produced 12 offset machines to begin with.
The success of the offset press set up an entry was for others to enter the field of printing. There were several adaptations of the offset process, including (but not limited to): perfecting (prints on both sides of the sheet at once) and web fed (feeds from rolls rather than sheets of paper) designs.
And furthermore, because the offset press removes direct contact between the plate and the paper, the plate actually lasts much longer. Also, because the offset press is a rotary rather than flat bed design, the production is actually much smoother and much faster. These kinds of enhancements have made way for photographic inventions of halftone photography, photolithography, and process color.
Offset Lithography Today
Offset lithography is by far the most common form of commercial printing. The process is a complex one. It works on a basic principle: oil and water do not mix. The plate has non-image areas that absorb that water. During this process, the plate is kept so wet that the ink doesn’t get on the wet areas and stays in the image areas. This is actually getting towards the end of the process. It starts when the image is output to film. For each color, there are separate pieces of film. Each piece of film is used to form a printing plate. The plate has non-image areas, which absorb moisture and repel ink.
The basic stages of the modern production process are: Artwork (which includes illustrations, photographs and text) are entered into a computer. These elements are put into a document using page design software (the most common are: Quark Xpress, Pagemaker or Adobe InDesign). The documents are then output to pieces of film using a high-resolution imagesetter. The images from these pieces of film are then transferred to a plate using a photochemical process. The photochemical process includes exposing the plates of high intensity light through the films and them chemically treating them so that the non-image areas are water absorbent. The plates are then fed to the press and the job of printing a job begins.
Now, there are glitches in the process. For instance, problems can occur within the platemaking process. If plates are not completely developed, this can cause residual coating on the plate, which can cause scumming on the press. Scumming occurs when nonimage areas accept a layer or uniform tint of ink.
Fogging can also occur. This is when negative plates are exposed to light.
When you move to the press, there are a whole host of other processes and procedures that must be followed. The lithographic press is complex mass of machinery that takes plates and transforms them into a completed paper product. There are several steps to completion, however. The process incorporates the following components: Ink: Lithographic inks are paste inks which are different than the relatively low viscosity liquid inks of flexo and gravure. These must be chosen properly for the particular substrate and final impression; Substrate: Must be properly selected for the type of press and natural of the desired final product; Presswork: This is the part where the paper comes in and all of the components are pulled together to form the completed product. Paper is brought from paper storage, ink from ink storage and the plates are mounted on the press. Ink is applied to the press and dampening systems are activated. This along with adjustments of ink, water and ink/water balance is called presswork. Presswork is the culmination of the components of offset lithography coming together to form the finished product.
The presses used in offset lithography are classified in terms of size, number of printing units (colors), what kind of feed they offer and whether they perfect (print on both sides of the substrate on a single pass through the press). Size refers to the maximum sheet width that may pass through the press.
The actual image size is determined both by the plate or blanket width and the plate or blanket length (which are limited by the cylinder diameter). A press smaller than about 12″x18″ without bearers (hardened metal rings attached to the end of the cylinder or cylinder journal) is called a small offset press but more often a duplicator. Duplicators started out as office machines. They are simple, but can be efficient presses. They are also very good demonstrating the offset process.
Larger presses generally have bearers at the ends of the plate cylinder in addition to larger sheet sizes. The Heidelberg KORD presses in our small pressroom have bearers, while the A B Dick and other duplicators do not. As a result the cylinders need to be packed to achieve proper impression pressure. A sheetfed offset lithographic press is one that feeds and prints on individual sheets of paper (or other substrate) using the offset method. A webfed offset lithographic press is one, which prints on a continuous web or ribbon of paper fed from a roll and threaded through the press. Sheetfed presses can run about 10,000-12,000 impressions per hour. Webfed presses can go up to 4 times faster (almost 50,000 impressions per hour).
For sheetfed presses, the units are connected by one or more transfer cylinders to transport sheets between stations. Must be an odd number to assure that proper side is printed. Each unit can print a different color, so that the number of colors is determined by how many separate colors can be printed anywhere on the sheet with one pass through the press. Hence, the number of colors is generally the same as the number of units.
The complexity of the printing press is why there are so many variable when dealing with the industry of printing period. There are a number of factors that can cause a job to turn out correct or incorrect. This is why in today’s industry, employers look for skilled pressman – usually looking to those who have formal education as well as on-the-job apprenticeship.
Electronic Prepress and Waterless Offset Printing
Prepress has always been a big part of the entire process. Prepress is where everything is prepared before going to plate and eventually on to the press. Traditional prepress involved paste-up procedures and many other outdate methods and practices. However, in today’s computer-based society, prepress has also become technological in nature. Computers allow the quick production of film, which is used to transfer images to printing surfaces.
Some printing surfaces can even be prepared directly by machines employing computer-controlled laser beams or diamond styluses. Images generated on computer systems and stored in databases can now be transferred directly to printing surfaces without any intermediate steps. As a whole, these changes have been called the prepress revolution. As this electronic age in prepress continues, the newspaper printing industry as we know it today will continue to evolve and grow. Even new presses today are continuing to run faster and be more automated, which will further enhance both the efficiency of the process and the quality of the product produced.
Another technological enhancement of the press and prepress revolution is waterless offset printing. Waterless printing is an offset lithographic printing process that eliminates the water or dampening system used in conventional printing. It uses a special silicone rubber coated printing plate, special ink, and typically a means of temperature control on press.
In waterless printing the process of printing is changed chemical one involving the use of Isopropyl Alcohol or their substitutes to a simplified mechanical process. Instead of the press operator balancing the delicate relationship between ink and water, all that waterless printing requires is a temperature range for transferring ink to the substrate.
The big advantage of waterless printing is that it uses inks with a higher viscosity. The benefit of that is that higher viscosity inks are thicker, and spread out less when applied to paper. When ink spreads across the page, it results in dot gain and loss of detail. Some dot gain is inevitable. Too much dot gain is bad, since it limits how fine a linescreen can be run.
Usually, a conventional offset press might have the ability to run 150 to 200 linescreen, a waterless press can run 300 or more. Linescreen is the friend of fine detail. Think of it this way: it’s a very fine mesh that the ink gets squeezed through. For reference, a newspaper will typically be run at a linescreen of 85 lines per inch and if you look closely you can easily see the individual dots with the naked eye. Magazines are often run at 133 lines per inch and you probably need a magnifying glass to see the dot pattern. Fine art prints will be run at a linescreen of 200, and they look like … well, fine art.
Waterless printing has many other advantages over conventional offset, as colors are more vibrant and the printed image sharper; however, the overall cost is slightly higher. The plate being made with silicone scratch easily so most waterless printing today is done on sheetfed presses.