The Work of the Stone Mason – Mixing Concrete and Designing Forms
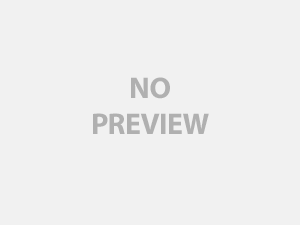
Cement masons must know their materials well. They must be able to judge how long different concrete mixtures will take to set and how factors such as temperature and wind will affect the curing, or hardening, of the cement. They need to be able to recognize these effects by examining and touching the concrete. They need to know about the strengths of different kinds of concrete and how different surface appearances are produced.
In addition to understanding the materials they work with, cement masons must also be familiar with blueprint reading, applied mathematics, building code regulations, and the procedures involved in estimating the costs and quantities of materials.
On a construction job, the preparation of the site where the concrete will be poured is important. Cement masons begin by setting up the forms that will hold the wet concrete until it hardens into the desired shape. The forms must be properly aligned and allow for the correct dimensions, as specified in the original design. In some structures, reinforcing steel rods or mesh are set into place after the forms are put in position.
The cement masons then pour or direct the pouring of the concrete into the forms so that it flows smoothly. The cement masons or their helpers spread and tamp the fresh concrete into place. Then they level the surface by moving a straightedge back and forth across the top of the forms.
Using a large wooden trowel called a bull float, cement masons begin the smoothing operation. This process covers up the larger particles in the wet concrete and brings to the surface the fine cement paste in the mixture. On projects where curved edges are desired, cement masons may use an edger or radius tool, guiding it around the edge between the form and the concrete. They may make grooves or joints at intervals in the surface to help control cracking.
The process continues with more finishing work, done either by hand with a small metal trowel or with a power trowel. This smoothing gets out most remaining irregularities on the surface. To obtain a nonslip texture on driveways, sidewalks, and similar projects, cement masons may pass a brush or broom across or embed pebbles in the surface. Afterward, the concrete must cure to reach its proper strength, a process that can take up to a week.
On structures such as walls and columns with exposed surfaces, cement masons must leave a smooth and uniform finish after the forms are removed. To achieve this, they may rub down high spots with an abrasive material, chip out rough or defective spots with a chisel and hammer, and fill low areas with cement paste. They may finish off the exposed surface with a coating of a cement mixture to create an even, attractive appearance.
Cement masons use a variety of hand and power tools, ranging from simple chisels, hammers, trowels, edgers, and leveling devices to pneumatic chisels, concrete mixers, and troweling machines. Smaller projects, such as sidewalks and patios, may be done by hand, but on large-scale projects, such as highways, power-operated floats and finishing equipment are necessary. Although power equipment can speed up many tasks, most projects have corners or other inaccessible areas that require hand work.
Various cement specialists have jobs that involve covering, leveling, and smoothing cement and concrete surfaces. Among them are concrete-stone finishers, who work with ornamental stone and concrete surfaces; concrete rubbers, who polish concrete surfaces; and nozzle cement sprayers, who use spray equipment to apply cement mixtures to surfaces.
Poured concrete wall technicians make up another occupational group whose activities are related to those of cement masons. These workers use surveying instruments to mark construction sites for excavation and to set up and true (that is, align correctly) concrete forms. They direct the pouring of concrete to form walls of buildings, and, after removing the forms, they may waterproof lower walls and lay drainage tile to promote drainage away from the building.
Unlike cement masons, however, poured concrete wall technicians generally get at least two years of technical training in such subjects as surveying and construction methods.