The World at Your Feet – for All Intents & Purposes It’s Been Flooring
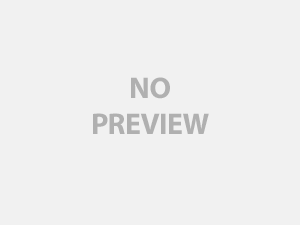
In situations calling for good hygiene, durability, safety and easy maintenance, the anti-static, anti-slipping and chemical resistance qualities offered by specific mixes can do much to meet these needs. This versatility makes it extremely popular across the whole industrial spectrum and is extensively used in the pharmaceutical, aerospace, retailing, engineering, sports and leisure sectors.
As resin flooring can be customised to address the different problems associated with specific industries, it is vital that plant owners discuss their needs with manufactures during the early stages of design and construction. Understanding a little of the process itself will help to make an informed choice.
What exactly is Resin Flooring?
The first resin floors were based on epoxy resins which have now been expanded to include many other different chemicals. These are mixed in liquid form in various combinations to produce specific floor types. The different components are mixed to a precise recipe that results in polymerisation or “curing.” The process is carried out on site and when performed correctly, results in a smooth, seamless finish far superior to the concrete base they are usually situated upon.
What you Should Consider
Resin flooring can be produced to a wide range of specifications so it is worth spending some time thinking about particular needs before approaching a manufacturer. This will not only ensure that the correct flooring is supplied, but avoid unnecessary confusion and possibly additional expense. Some useful questions to consider are:
How much traffic is the floor expected to take and to what intensity? Light duty is considered to be moderate foot traffic and occasional rubber wheeled vehicles. Heavy duty could involve the constant use of fork lift trucks, hard, plastic wheeled trolleys and some heavy impact from plant machinery or loading bays. These extremes call for different floor types, so assessing the amount and type of traffic is crucial.
Will loading take place from the floor? If this is the case, whether static or dynamic, the severity of impact needs to be considered.
What chemicals, either through manufacturing processes or cleaning materials will come into contact with the floor? Resin flooring can be made to withstand chemical attack, but this must be clarified at the planning stage and any specialist cleaning compounds should also be mentioned.
Does the floor need to comply with industry specific regulations? Pharmaceutical and food industries for instance call for a high degree of hygiene and almost certainly require non-slip surfaces. Anti-static and a cosmetically pleasing appearance may also be points to consider.
Temperature and Heat Exposure. If the flooring is to be subjected to extremes of heat or cold this needs to be mentioned, as should any possibility of prolonged, direct sunlight or ultra-violet light.
Refurbishment. Floors laid on an existing base may react to previously used sealants and other chemicals. Give the supplier as much information as possible at the planning stage to avoid costly incompatibilities. This should include age, previous usage, and any known chemicals or finishes used.
Aesthetics. If the cosmetic appearance of the floor is important, this should be made clear from the outset. Resin floors come in a wide range of colours. A texture effect can be achieved by adding flecks to the mix but this must be discussed with the supplier beforehand.
Timing and Accessibility. Components are mixed on-site so sufficient space needs to be made available for mixing and storage. Adequate time must also be set aside to allow for thorough drying and curing of resin and any base screen.
Cleaning & Maintenance
Resin floors are extremely durable and with proper care and maintenance should last in excess of twenty years. Cleaning will depend to some extent on the type of floor and its purpose, but generally a mechanical scrubber with a wet vacuum is the most suitable. A mop and bucket is not recommended!
If a high degree of hygiene is required a bactericide solution can be used with pressure washing at 60-80 degrees centigrade.
Corrosive chemical spillages should be cleaned up at once. If damage does occur then this should be immediately repaired to prevent further spreading. Mechanical damage should also be repaired not only to prevent worsening over time, but for health and safety reasons.