Tips for Surfacing Wood to Achieve Smooth Surface
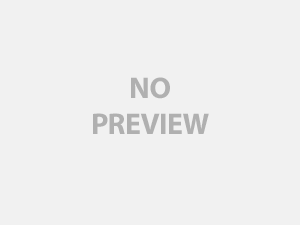
To achieve the smoothest wood surfaces, it is generally better to surface each component before it is installed. Indeed, some pieces must be surfaced in order to fit. Others must be surfaced to eliminate saw cut marks, raised grain resulting from exposure to moisture, and damage suffered during transport. Smooth surfaces also result in neater and much stronger joints.
To achieve consistently good results, follow two basic rules: always use sharp tools and study the grain of the wood and work the surface accordingly.
You will need a variety of tools and materials: hand and power planes, a jointer, files, rasps, plane, sandpaper, and scrapers. A selection of surfacing tools are: wood-body smoothing plane, metal-body jack plane, sanding belts, sanding accessories for drills, orbital finishing sander, sanding block and sandpaper, portable power planer, block plane, spokeshave, scraper plates, plane, assorted rasps and file, triangular files and rifflers, and two-sided rasp. For surfaces that need filling or building up rather than planning down, add wood putty and liquid sealer-fillers to the list.
Maintaining a Keen Cutting Edge
Always use sharp tools. Tools with metal edges should be sharpened on a whetstone. If the blade is very dull or misshapen, dress it first on a grinding wheel, being careful to maintain the original beveled angle. Move the blade back and forth across the wheel using light pressure. Don’t press hard enough to generate heat, or the temper of the edge will be lost.
A two-sided whetstone is used for sharpening and then honing the edge after grinding. Increase the original angle of bevel slightly as you hone.
With normal use, tungsten carbide blades will outlast high-speed steel ones; therefore these more expensive blades are more economical in the long run.
Working With Grain
Reading wood grain is simply a matter of observing whether it runs lengthwise or crosswise. Except when working with the end grain, all surfacing is done lengthwise. Before surfacing the face or side of a board, observe the direction of the grain. Then take a closer look to determine which way is uphill. Although boards with a grain pattern perfectly parallel to the surface can be worked either way, most boards are best worked in the uphill direction. This allows the cutting or scraping tool to cut the wood fibers rather than break them. The result is an easier job and a smoother surface.
The end of the board can be smoothed in either direction, since the end grain is non-directional. Use sharp tools to avoid compressing the wood fibers and opening spaces between them; this makes the surface rough and porous. It is also important when working with end grain to avoid splitting. Clamp a piece of scrap wood to the edge of the work and let that piece split instead, or make a small bevel (called a chamfer) along the edge. The chamfer method is best, provided you can smooth the bevel later by trimming or surfacing the length of the board. A third method is to work from each edge toward the center of the piece. It is difficult to get a really square surface by this method, but it does prevent splitting.