Tips on Making Welt for Furniture, Industrial, or Marine Upholstery
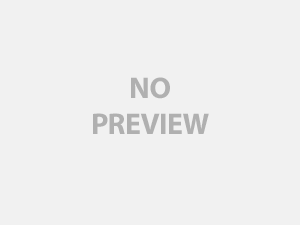
When it comes to making welt you have your fiber welt for furniture usage, a very skinny plastic welt used for car upholstery, and a larger plastic welt used for car and boat upholstery. The fibrous welt is very simple to cover in fabric but much more challenging to cover in vinyl. Using a welt foot helps tremendously, and if you don’t have one, it’s highly recommended that you invest in one, since almost all upholstery jobs require welt to hide seams.
A welt foot is a large flat foot for an industrial machine which has a slit carved into the center of the foot. The welt cord itself is positioned into the slit while the machine sew the fabric or vinyl beside it. The closer you sew to the welt the more professional the finished job will look, but if you get too close, you’ll snag the welt and it’ll be easily visible if you try to use it on the upholstery.
If you stay too far away from the welt cord while sewing you’ll get a loose welt covering that looks sloppy and will wrinkle and roll. Finding just the right distance to sew next to the welt is, as previously stated, much easier with a welt foot. If you don’t have a welt foot use a zipper foot that will still allow you to get relatively close to the welt.
Don’t attempt to use a regular walking foot to make fiber welt for furniture. The foot is heavy and crushes the welt cord making it look flat and odd. Rolling the welt back to a round position is time consuming after it’s covered in fabric. Also, you may think you have it worked back into a rounded look for the welt, but within no time, the customer will notice at home that their welt has gone flat – there’s really no fixing it after it’s smashed flat. A regular foot can be used for plastic welt but it can still damage the welt and it won’t give as much of a professional look to the welt as will the zipper or welt foot.
When working with plastic or fiber welt and vinyl you’ll notice that the vinyl is not pliable, making it difficult to turn corners. Upon turning corners you’re stuck with a wrinkled look right at the corner that’s unattractive. You’ll find the wrinkled welt corner on many items you purchase directly from the factory, but to eliminate it, make small cuts in the welt leading up to and beyond the corner.
Just as you’re approaching the corner, use your scissors to make small cuts in the vinyl, from the edge of the welt wrapping to just before the stitching. Make these slits, every inch, for a few inches before and a few inches after the corner. Now when you turn the corner the welt will fold directly on the corner and will eliminate the wrinkled corner look.
Upholstery work is fun and challenging but you’ll want to take the time and expense to do it correctly. Invest in needed tools, implements and attachments that will make the job easier and more professional-looking. Some tools of the trade may seem expensive but most are one-time purchases that are well worth the investment.