Understanding the Process of Quality Control
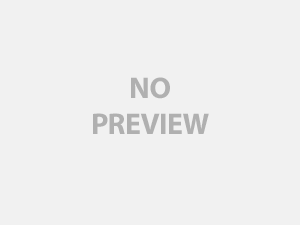
When the issue of quality for printing is discussed, there are specific set of needs that must be met. First, the most obvious one is that the customer’s needs must be met. Second, providing a certain level of customer service along with an excellent level of quality. Third, meeting or exceeding the level of quality produced by direct competitors. Fourth, meeting internal specifications for quality with consistency and adherance to company printing policies (with consideration to waste issues, run numbers, etc.)
Quality control starts at the top. This has a lot to do with the mindset of upper managment. Managment must be sure to sure that it is committed to quality control as it relates to production needs. Implementing a quality control program starts by coming up with a policy. This should always be a written policy and it should be clear about the expectations of the company and what kind of rules and regulations are instituted by the quality control program. Part of the policy should also be the definition of quality. What does quality mean to your company or organization? How will you know when achieved an acceptable quality on a specific product?
Upon beginning your quality program, the next step after establishing a written policy and talking with company members about general company objectives is to organize your program. This usually begins with the organization of a “quality department.” There are four questions that this committee of people can ask to sum up the present quality evaluation process: are we currently printing it well?; have we printed it well in the past?; will we always be able to print it well?; and could be we doing a better job of printing it?
Usually, the answer to that last question is yes and it the quality control committee that institutes policies and procedures within the organization to make that happen. Most printers would acknowledge that they learn from trial and error. However, a quality control committee can evaulate past errors or ideas and come up with set procedures to ensure good quality.
Quality control has long been considered a technical subject and procedures regarding it have often been given by people who do no consider the human error aspect to it. Phillip Crosby, a well-known author, points out that falling back on basic management procedures is the first step to implementing a successful quality control program. The foundation for such management principles is as such:
quality will be defined as “conformance to requirements”
that “the system of quality is prevention”
that “the performance standard is zero defects”
that success in attaining quality is measured and compared with the “price of nonconformance”
The first concept defines quality, which again is something most print companies have a hard time doing. The second concept characterizes the ultimate objective for a quality management program; the third concept describes the standard of performance; and the fourth provides the ultimate way to measure quality. Together, these factors provide the platform for launching an affective quality control program.
Other steps to be considered when setting up your organization or company for quality control are as follows:
planning
setting objectives
organizing a committee
setting standards for conformance
installing systems of measurement
strategies for taking corrective action
strategies for shifting emphasis to preventing nonconformance
educating all levels of management
the installation of an incentive program
determing the true cost of nonconformance (re-runs, make goods, remakes, water, staff time required for handling customer complaints and coordinating follow-up and the cost of the current quality control system (if there is one in place.)
How can print quality be measured? A printing press is great measuring instrument. It can test the runability and the printability of the paper. It can visualize fit and register. It can demonstrate the purity, strength, lay-down and drying of inks; and check the running characteristics of plates. When checking a press sheet, the quality control committee can determine whether or not the color being presented is correct, whether the color film was selected by the stripper, see if the page sequence is correct; and even check whether the job is bindable.
One of the best ways for a printing company to institute a successful quality control program is to do it from the beginning. On-going costs for preventing poor quality from happening rarely exceed the all-inclusive cost of reprinting jobs and the penalities that are usually incurred from an unsatisfied customer.
A zero defects program is one way to be preventative. A Zero-Defects programs work like such: Emphasis on zero defects reverses the philosophy of controlling quality through rejecting and discarding substandard work. The aim of all involved from pressman to managers is produce conformance quality work by eliminating errors that can be made by anyone involved with selling, planning and printing a job. Introducing zero-defects is relatively easy and have been proven to work relatively well.
This is because the mission of the program is clear to all involved. There are no longer vague references to quality control – the goal is much more clear and concise. The standard is do it right the first time! Also, everyone is completely committed to the program and it trained and encouraged to spot for errors. They are directly involved with coming up with ways and means for preventing the kinds of problems that would lead to poor quality and ultimately the dissatisfaction of the customer.
According to the philosophies associated with this program, there are two major causes for errors: lack of knowledge and lack of attention. When you are dealing with a lack of knowledge, that can easily be solved. Companies can provide education and training that will be required ot help develop quality skills.
However, when you are dealing with a lack of attention, that is far harder to fix. Lack of motivation and weakness in one specific area are all core reasons for lack of attention. Strengthening supervisory skills, getting top management’s support, and clear policies and procedures can help to alleviate that lack of attention.
A typical zero defects program consists of four functions: organization, planning, promotion and follow through. If all politics and functions are followed, the concept really does work. Management, consistency and the talent to institute the program will ensure its success. The workers will understand that zero defects is your firms actual quality objective if mangement plays it roles with committment and conviction.
Quality control takes all hands on deck and ensures the lifeblood of the printing business. If everyone from upper manage to the printers to the press crew were involved with a quality management initiative, the printing process would by smoother as it relates to customer satisfaction. Gone are the days when quality control was a vague and undetermined issue; now there are policies and procedures in place that have worked across the board and everyone can have a say in the quality program. This will make for happier and more productive workers who can put out products with pride and it will definitely make for happier and more satisfied customers.