Wooden Houses: The Future?
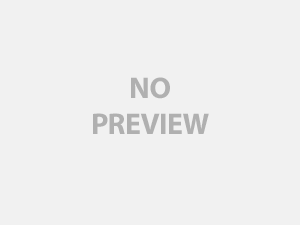
By Steven Lambert
Wooden houses could be an answer to the lack of affordable homes today. If we could build a mass of wooden houses, along similar lines as the prefabrication plans of the 1940′ and 50’s, it would solve many problems.
Prefabs
Wood as a building medium is one of the most flexible and diverse we could ever imagine. With similarities to man made materials such as concrete and Fiberglas. It strength comes in the way the fibres are woven together and the resins that are soaked into it. As a construction material it is strong both in compression and contraction.
After the second world war, 160,000 prefabs were build to ease the housing problem in Britain. At the time they were thought of as a temporary answer to the housing problem, but still to this day, hundreds still remain standing.
In London housing has reached such a crisis point, that the Mayor, Ken Livingston, has decided to look into the idea of prefabs to ease the problem. These are public service improvement targets, as well as the Deputy leader: John Prescott’s promise to build millions of new houses in the next 10 years.
Around London the price of an average home, even for a first time buyers, start at $140,000. This would need an annual wage of $47,000, to meet the minimum of mortgage requirements. The National Housing Federation, has shown that this is far outside the scope of most ordinary people. So something has to be done.
There is still a prejudice to the idea of prefabs, as they do hold the stigma of being for the poor working class. Today, they are more referred to as Modula housing. They are more likely to come as flat-pack homes, factory made to be dismantled and reassembled elsewhere. The number of people expressing an interest in these schemes, are in their hundred’s of thousands with growing responses from the housing associations, who put the prices within feasibility.
The construction of modular building can be made easier with wood on site. But in Poland, they already have factories to turn them out, ready to be shipped anywhere in the world. Already on wasteland in Stockwell, in south-west London; the $700,000 project is going ahead.
Many of these building will use the SIPs system (structural inserted panels). These are pre-build panels, built off site to fit straight in the buildings. These modern techniques allow flexibility, speed, but with a high degree of quality.
The Forestry Stewardship Council (FCS) set the standards to which the wood is grown. Primarily, the ecological requirements that would grow the product, with little impact upon the environment. Keeping in mind, that this is a business, and has to make a profit.
One challenge faced by wooden manufactures, is the tendency of the material to twist and warp. This can be overcome in house construction, by the use of compressed timber particles, and composite panels are used to build up a joist, for strength.
Using wood as a building material cannot be equalled. It provides the strength and flexibility for house building with costs so low, they out perform any other type of material used in the industry.
Growing wood for the building industry, would provide so many benefits, it is surprising the schemes have not been taken up long ago. Here is something which could be grown within a reasonable distance of the site of habitation and construction. Of course this could not be done at any cost, and must be considered with the guidelines of the Forestry Sustainability Commission.
Forests
Forests are the key part to any building project concerning wood.
Commercial plantations are the most realistic way of obtaining the required amount of material to feed the industry. To this end, many countries are planting new forests to meet the need of a growing demand.
There have been many objections to wide scale commercial logging, but the industry has responded with a balanced approach. In the US, many companies use a credit system, which reflects how environmentally friendly they really are.
The 3 main points of Green Credit scheme are:
1 Salvaged Products
2 Recycled Content
3 Certified Wood Sources.
Salvaged Products
This uses grades of wood, as well as recycling, to monitor their performance. So the whole scheme is geared to forcing the companies towards a greener approach. Grades of wood are taken into account, as the industry does have a reputation for only wanting the highest grades, and little else. If this was to be judged by quality and standard, only high grades would be used. But with MDF and fibre board, even the lower grades and waste can be used. Salvaged wood plays a large part of this, and can add to the Green credit programme.
Air Quality
Forests are now monitored in many parts of the world, as an indication of Air Quality. A negative air quality reflects badly on the population. The US Environmental Protection Agency, and the American College of Allergy, Asthma and Immunology; say people spend 90% of their time indoors. So air quality is a high priority. Forests are the lungs of the world, and poor air quality here can reflect badly on the rest of the planet. Whereas better ventilation is the answer to building regulation, the air has to be of a high enough quality to begin with.
The process of logging will have a massive impact on the environment. Any extraction of raw materials should take into account Air and Water quality, as the felling of a forest can have wide reaching implications for a whole area. But even the cutting down of a forest can have less harmful effects on the environment than that of the production of concrete or steel. As it holds the prospect for lower green houses gas emissions, and consequently will have a smaller effect of Air and Water quality. None of which can be guaranteed by other building materials.
Landfill is one of the biggest problems, resulting from house building which uses brick; concrete, stone and steel. Wood does not pose any problem, as the product is totally recyclable, and can be said to have many lives. Even sawdust, can be used in some products. New wood fibre has its obvious uses in building, but sawdust and shavings have to viewed as recovered material. Any material which is recycled at this point of manufacture, goes a long way to helping the environment. Any recovered material from the manufacture process, can be used for particleboard panels and moulding, which go towards MDF.
Green credit system
The Green credit system, carries out a third-party audit in the US industry. One organisation is the Scientific Certification System (SCS). They monitor recycled contents of products in the industry, to back up any claims which might be made by a manufacturer.
Certified Wood products fall into two categories. One is the forest management certification, and the second is the chain-of-custody (COC) certification.
COC is a document, which travels with the wood, to prove where it has come from, and can be traced back to its source. They come up to a standard of guidelines and principles, set down by the organisation. The main reason for this, is to make sure that certified products are not mixed in with un-audited ones. Providing guidelines for COC wood, goes some way to helping Architects, Contractors and Project Owners. Proving they take seriously the need to offer a guarantee of proof, from the vendor.
The Forest Stewardship Council (FSC) caries out the chain of custody, from the forest logging process to the sale of the wood for the building industry itself. These are done with the accreditation of bodies such as the Soil Association, which have done a great deal to bring a Green standard to the world. In the US, another body for regulation is the Sustainable Forestry Initiative (SFI), which monitors 96,400,000 acres of forest.
So a great deal of wood manufacture and processing, only poses an environmental impact, in terms of transportation, between processes.
In the US, building salvage is referred to as: rediscovered wood. This mostly takes the form of flooring panels and tiles. But their use, greatly adds to the system of green credit, awarded any firm using them. In Baraboo, Wisconsin, The Badger Army Ammunition plant, holds 4,000,000 board feet of lumber, this is enough for 300 homes. The Green lobby are at pains to make sure the wood is used again, as this saves the cutting down 17,000 trees!
Here is a good example of how the wood was judged in quality. The whole site contained a very high quality of wood. The characteristics include old growth wood, with few knots. Giving tight growth rings of high density. The American companies involved in this type of projects are Scientific Certified Systems (SSC) and SmartWood. They have gone a long way to proving that Green credit reward systems can work, if used on a salvage project.
Another example is the California’s Collaboration for High Performance Schools (CHPS) program. If the value of the material used in a building project is: $100,000 then 5% had to be salvages, or rediscovered, to earn one point in the credit system.
Paper is a large area, when recycling is used to gain green credits. As most of it, will have been recycled.
The souring of wood is the most important part of ensuring that the COC, has some validity. The bridge between the environment and business has been greatly helped with such non-profit making organisations such as METAFORE.
Guidelines, are the main point of the Green Credit scheme, giving consumers and industry some ideas for the future. As yet, the financial implications, may be beyond many companies. Already these guidelines have helped in the implementation of Green building standards, being set by many countries. Life Cycle Analysis (LCA) plays a large part in those guidelines. Even though many of these schemes are voluntary, they have seen an increase of 35%, in the last year.
One of the main concerns with the forest Stewardship Council, is the problem of illegal logging. Often illegally obtained wood, will be mixed with certified wood, to launder it through the system. Once the trust has been broken, it is almost impossible to tell them apart, so they can only be tracked and traced at source.
Architects and builders often prefer high Grades of wood. These have to be obtained from forests with a sensitive effect on the environment. If other grades of wood are taken into account, they can be extracted from less sensitive forests, with a lesser impact. High Grades, often means that the best and most mature trees have to be taken from the forest. Industry likes them, as they have predictable properties, and easier to process through the manufacturing process.
When building a wooden house, the clear wood planking on it’s sides, are the most important look to the house. This special look, has caused more problems for the grading of wood, than anything else. If it contains knots and distortions, it is classed as second best. So no logging company will go out of its way to obtain that type of wood, for that purpose.
If alternative designs of buildings are taken into account, the high quality of this clear wood, would not be such a problem. Architects and designers, could find a way round the problem, and free up the need to only offer high grades of wood to do the job. This would have a knock on effect on the logging industry, as they could quite happily fell and supply timber, knowing they are going to sell it, and not face rejection.
The United Nations Food & Agriculture Organisation, published a report in 2000, stating that South American countries will lose 11,000,000 acres a year to deforestation. It is not realistic for these countries to stamp out logging altogether. Even if they agree to set aside areas of special scientific value, they will still need to face up to the effects of logging as a valuable commercial asset.
When a large commercial logging company goes into a Forrest, they have to strip out all the trees, in order to obtain the high value grades of timber. If the forests are managed more responsibly, wood of commercial value can still be taken from the area, with less environmental impact. A typical forest area, only holds 5% of timber that is of any commercial value. Once this is put into place, the forest can go back to having a violable ecosystem for the future.
Another approach is to experiment with non-traditional, and lesser know species. Some of these are being used in the commercial market, and as the industry expands, designers are beginning to take a responsible approach. If these lessor known products are looked into more, then they stand a good chance of being embraced in the commercial market.
Large scale forestry may be feasible in some parts of Britain, but not over all. There are many consideration to take into account, when it comes to soil types. What is more, growing trees on an area, may add to the soil problems, as in the water run off from pine.
Skilled Workers
When it comes to building techniques, working in wood offers more opportunity to unskilled and semi skilled people, than other types of building material.
It is a more forgiving medium to work with. A piece of steel, once ordered from the foundry, can only be dealt with once. If a mistake is make, it can only be returned for scrap. Off cuts and cut down pieces can be reused in some ways, but generally once a piece of steel has been cut to the requirements, it can no longer be used for anything else. Wood, on the other hand, can be used for many things.
From beams and joist, to floorboard and panelling, wood can be used to work in many different ways. It is cheaper than steel, and much easier to manipulate. The tremendous heat which is needed to weld steel makes it unforgiving when it comes to production. It is an absolute medium.
Stone and brick are so inflexible, that once set in place, they cannot be used for anything else. Wood on the other hand, offers so much more than recycling off cuts.
Medium density board, and compressed wood, is used more and more in the building industry as a way of overcoming the more tradition problems of solid wooden pieces. The is less distortion, so it is less prone to warping. This makes it of a higher standard, than old fashioned timber lengths, and can finally come up to the standards required for the precise building industry. Because there is less predictability in its movement, MDF can be employed with a lot more certainty, and can be relied upon to do the job asked of it.
Medium Density fibreboard
MDF is wood based composite material. The main difference between it, and other forms of composed wood materials, like plywood and chipboard, is that it is made from fine wood particles. Other forms of boards, are simple chipped wood that has been pressed together to give the best effect. MDF differs, in that it is pressed together under steam, to form the particles into one solid mass. It has been broken down to fibre tracheids vessels, which are the very cells which make up the wood.
This makes it strong, flat, rigid and useful for any amount of ideas for construction. It can be cut in anyway, as it does not contain any grain or knots within the wood. In fact, each piece is uniform and guaranteed to perform in a predictable way. Because the surface of the board is uniform, it can be easily painted, to give a smooth surface. Having no grain, means it can be machined, and drilled in several ways. It works well with water based paints, as well as a variety of veneers and laminations.
Disadvantages of using MDF
However, there are many problems with using this type of material.
The biggest is from the dust.
After processing, MDF contains a chemical called Urea formaldehyde, this can cause irritation to the eyes and lungs.
If the boards are properly machined in a well regulated work shop, there is little danger, as safety precautions will mean the shops are well ventilated and the workers are wearing the correct protective masks and goggles. There are types of MDF on the market which are Urea free, such as Medex and Medite 2.
Problems are not just restricted to the hazards to workers. The material contains a great deal of glue, and this can cause damage to cutting edges, as saws will become blunt.
When considering any construction with MDF, you have to take into account, that if joints and connections are made at a weak part of the wood, this may crack and break. So when drilling holes, they have to first be made by a pilot hole, then ensured that they are well in from the leading edge of the wood.
Painting is the best way of sealing in any harmful chemicals, so any application is best done to cover the wood completely.
Debarking
Any type of wood can go into MDF manufacture. Here we have to take into account, that in order for it to be used as a commercial proposition, it has to come up to a reasonable standard. So the logging process, can take into account the debarking of the log and even include this in the finished product.
However, few manufacturers like this as it can cause problems latter on. First of all, it can make for problems in the equipment, as it would contain a certain amount of grit. This can either blunt the cutting edges of the machines, or cause breakdowns in the process line. So the most popular type of debarker used for this is a Ring Debarker, although Rosser and Drum ones are also used.
With feeds of up to one tonne per minute, the Cambio Ring Debarker, can handle logs of up to 2.5 metres in length. With concerns about damage to the logs in the process, this type of Ring Debarker, does little harm, in the method it carries out the debarking. Held in place by pneumatic or spring heads, the tools rotate around the log to strip off almost all the bark. However, we have to keep in mind that many of these machines are diesel operated, and do contribute to greenhouses gases.
Chipping
The logs have to be broken down into chips before they can go through the process of being turned in to MDF panels. Some plants accept chipped wood straight from other sources, but most chip the wood themselves.
Disc chippers are typically used, the size and formation of the blades, dictate the size of the chips. Too big, and they are re-chipped; but too small, and they may simply go for fuel. High stocks of chips are carried, to ensure the right blend, for the correct product. High moisture resistant high density board, for example, would hold 10% Eucalypti wood.
After washing and screening with a magnet, the final process of chipping is checked over to maintain a high standard.
Pulping
Defibration, is the process of breaking up the fibres. Breaking them down, to be manipulated for manufacture. This goes through a course of expansion and contraction, until the wood pulp is metamorphasized into something completely different.
Being compacted into small plugs by a Screwfeeder, the chips are heated to soften the wood for 30-120 seconds. Finally they can be fed into the Defibrator. This is a very powerful grinder. Which pressurises the pulp between two rotating bladed. Rotating against each other, they break down the wood pulp into finer particles, the closer they get to the edge of the blades, through radial grooves.
So the plugs are fed through the centre, to be spread out by the centrifugal forces, spinning outwards. Here to be pressurised and heated to 150C. Lignin and cellulose, are the cement which binds wood together. Once this is broken down, the process can move on. After only one minute, the steam is separated and the pulp is passed through the first process of the Defibrator.
The level of freeness, of the fibres, has to be determined, and the pulp may have to go through a second refiner. But by now the pulp is of a fluffy, fine and light quality.
The Blowline
The Blowline is a process by which the fine pulp is passed through a 40mm hole at high velocity. Here wax is added to help stop the fibres from bundling up, by keeping it wet. Hydro-bonding can be a problem in the process at this stage.
Now it expands to 150mm to be heated by coils of up to 550f. The air-fibre ratio is about 500 cubic ft/lb.
Mat formation
A Pendistor is a process which makes sure the MDF has an even and smooth flowing surface. The previous processes can make the finished products random and uneven. Falling on a conveyer belt, impulses of air, make sure it flows down to a vacuum box.
Pressing
The most important feature of MDF, is its incredible strength, without the sacrifice of weight. So the achieving of a good quality density profile, is vital in this stage of the process. Pressing the product into a smaller area, ensures that you can achieve the right kind of density.
Pressure can reach 3500 MPa and be heated to over 200C, with steam or even radio heating.
Finishing
Finally they boards are allowed to cure, to ensure the setting of the resins. After that they can be sanded or sent to the next process, which may include the addition of veneers.
Oriented Strand Board
This is a construction panel made with layers of precision-manufactured wood strands. They are pressed with exterior grade adhesive resin. Based on the older form of waferboard in the 1970’s, this finds it’s strength in the way the strands are oriented. The combined layers of large mats are subjected to intense heat and pressure to be formed into a master panel.
Insurance
When you look at the wooden housing problem as a whole, you begin to wonder why it has never taken off? Certainly in the US, wooden houses are built with little problem, but not in the UK. Why?
Composite wooden structures can overcome some of the more traditional problems of the material, with the use of applied chemicals.
Fire and rotting, have always cast a shadow on wood, as a serious medium. With new fire retardant chemicals on the market, wooden houses can now overcome one of the main problems preventing it from being taken seriously by the insurance market.
Weathering has always taken its toll on wooden structures, and traditional wooden houses have not proved reliable in the long term. But composite and compressed forms of wood, can be treated with new chemicals to prove that it can come up to the standards of brick; stone and steel.
The problem is insurance. Few banks and building societies want to take on the financing of a wooden house. There are two main reasons for this.
1. Fire
2. Weathering
Wooden houses were banned from being built in London, after a series of great fires. Stone and brick proved more reliable. But in this day and age, we can turn to techknowledgy to save the industry.
Fire retardant chemicals can be added to the wood at the MDF stage, and certainly this can yield good results. However, this does have some negative effects, which effect any experiment, undertaken by building standard experts. They have proved that these very chemicals can damage the house in the long term.
One of the worst effects is rotting. The chemicals may lead to microscopic gaps appearing inside the wood. This would let in water, which leads to rotting, and the rusting of any metal part used in the wood, like nails; screws and brackets. A far more serious down side to fire retardant chemicals, are the fact that they can lead to the weakening of the wood. Resulting in no wooden building being erected more than one storey high.
Hope is in site, in the form of fire retardant paint.
These do not pose the same threat to the wood. They do not enter the structure of the wood, in the same way as other chemicals, and even form a seal around the wood. Fire experts have proven that if a good seal is kept around a piece of wood, in reconstruction, then when the parts are added together, you end up with a very safe house. Wood only ignites once it has a flammable surface. So in other words, if the wooden panel is sealed, it is guarded against the fire raging around it. Certainly it would not withstand the same punishment taken by brick and steel, but it does have other advantages.
Steel will buckle and warp under extremes of heat. Wood burns at a constant, and can prove to be reliable in such a situation. Firemen know where they stand with a wooden building. It either burns down or it does not. Steel and brick buildings can hide hidden dangers, which only become apparent, when the personnel go inside.
All together, the future looks bright for wooden houses, and wood as a material, can only go forward.