Wool Manufacturing Process
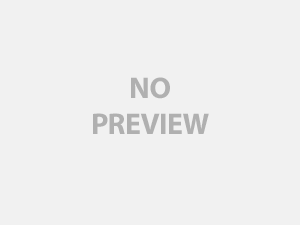
When wool for wool manufacturing comes to the factory, it is quite dirty. Raw wool comes to the factory fresh off the sheep, and the wool manufacturing team must sort and grade the raw wool before it is cleaned. Since sheep are sheared once a year, a variety of sheep age and quality are used for wool manufacturing. Grade depends on breed of sheep mostly as well as how well the sheep was raised. The attributes of wool quality are crimp, length, strength, color, and the fineness of the fiber. Fleece is picked through and sorted through by people who are a great asset to the wool manufacturing industry. They have an eye for stained wool or wool with debris as well as which wool would blend best in the wool manufacturing process with other fleece from other lots.
The next step to the wool manufacturing process is called scouring. This is basically the process of cleaning wool. There are machines that are used for this process, and then the wool is soaked, bathed twice, and rinsed. The scoured wool is then dried and baled for further wool manufacturing processes.
The third step in wool manufacturing is the removal of lanolin. Lanolin is grease that is in the water where the wool was scoured. It is kind of nasty when it’s being skimmed from the water, but it is quickly washed and used in a centrifuge, bleached, and filtered. Lanolin is used in shampoo, makeup, and hand lotion, and it’s an important part of the wool manufacturing process.
Next, the wool is often dyed. Some wool manufacturing requires dyeing at a later stage, but for most higher-end wool fabrics, they dyeing process takes place immediately after baling. Some wait until the wool is fabric to dye, but this is not always recommended. It used to be that wool fiber was dyed by hand, but the wool manufacturing process today requires the use of machines and automation.
Carding is the stage before wool becomes yarn. The fibers are combed, similar to when they are spun on a spinning wheel, and they kind of look like a web. Of course, this wool fiber is not very strong or taut. It is called roving. This wool fiber is rolled up on a large spool and sent to spinning. Some people add things to the roving to make it suppler to work with. This is what gives roving a cloudy look.
The spinning stage of wool manufacturing forms yarn by twisting up the roving taut. This is a quick process done on a spinning frame. After it’s spun, the wool manufacturers steam it and store the bobbins while they wait for it to be woven into fabric.
You may think the wool manufacturing process is over when the wool is woven into fabric. Most often, an automated loom is used to interlace the yarn. The typical size of a manufactured bolt of unfinished fabric is 72 yards.
The final stage to wool manufacturing is finishing the fabric. Unfinished fabric looks shoddy right off the loom, so it is fulled. Not all types of fabric have to be fulled, but wool pills very badly if you do not. In a trade-secret process unique to wool manufacturing, friction and heat along with moisture and pressure shrinks the wool, and then it is cleaned. After this, it is sheared even so that the texture isn’t rough. When indicated, some of the wool is napped on the edges.
After the wool manufacturing process is over, it is up to designers to come up with fabulous ways to use the wool. Wool is a favorite medium for sweaters and blankets, rugs and even accessories. Wool manufacturing is key to the economy of many communities, and its several steps employ many people. It has come a long way from the spinning wheel, but wool is one of the most natural renewing fibers found today.