Difference between Calibration and Validation
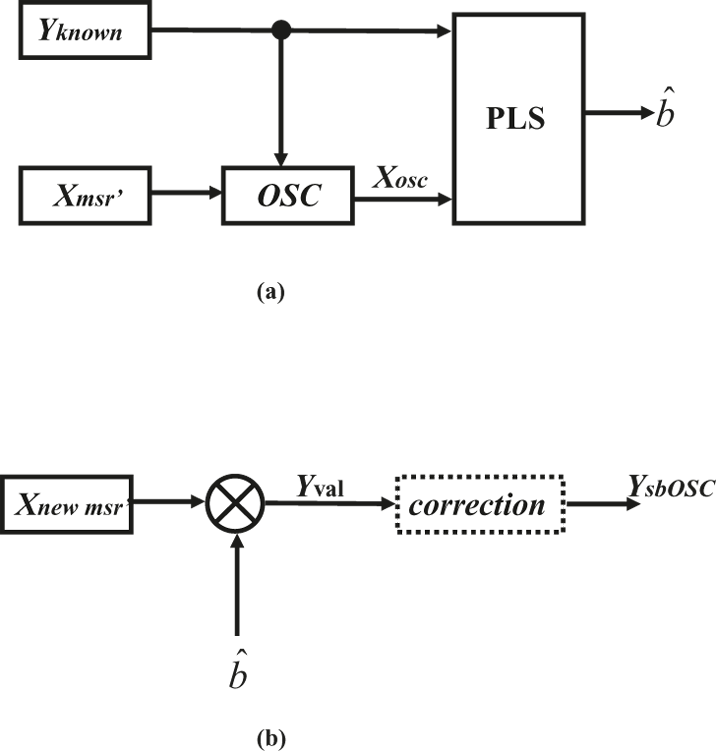
Calibration and Validation are the main processes that ensure the quality of a particular product. Both processes have slight differences in the way of judging a product’s quality. In calibration, a product’s quality is measured with accepted references. In validation a product’s quality is being checked with general parameters of operating and confirming an item’s performance and quality. Both procedures are an essential part of manufacturing and are also used extensively to check the level of quality of different items. Mostly, if you are checking the quality of different instruments, the most commonly used method and procedure is calibration as you need accurate results from checking. Other products which do not need accurate quality checks can be tested through the validation process. You only check whether a system, service or a specific product meets all the requirements by following exact specifications.
Instructions
-
1
Calibration
In calibration, a product’s quality is measured with an accepted reference or an item that has been tested before that meets all the required criteria, requirements and specifications. In products like different kinds of instruments which need pure accuracy when it comes to quality, the calibration process is applied. For example, your manufacturing source is making different kinds of electronic instruments which need pure accuracy in all circuit related specifications, so in order to check the quality you will compare them with instruments which are already being used. The manufacturer will make sure on their end that all the instruments must be equal and pass the quality assurance department. Essentially when you check any product’s quality with an accepted reference of measurement, you call this process calibration.
- Image Courtesy: biomedicaloptics.spiedigitallibrary.org
-
2
Validation
In Validation, a product’s quality is checked with general parameters of operating and testifying to an item's performance and quality along with its overall specifications. Some time, a third party also validates and checks a product’s quality and level of performance. Even your supplier will also appreciate it and gives you confidence to check the quality level of a specific product. You can also categorise the validation process into four further parts that include prospective validation, retrospective validation, locational validation and concurrent validation.
- Image Courtesy: annals.org